There are 4 basic welding positions you will encounter as a welder. These four are designated by numbers from 1 to 4. Number 1 represents the flat position, number 2 the horizontal position, and number 3 represents the vertical position.
Number 4 refers to the overhead position. For this article, we are going to be discussing the 3F welding position. And as already mentioned this refers to welding in a vertical position. The F in the name refers to the type of weld, which in this case is a fillet weld.
What is The 3F Welding Position?
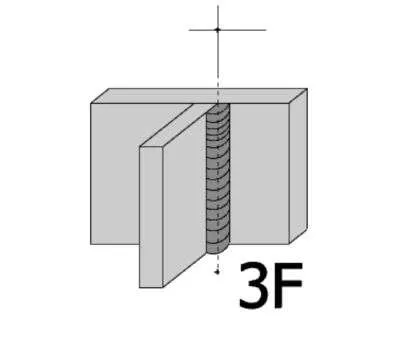
A fillet weld is a type of weld used to join two metal pieces in a triangular cross-section. As such, the 3F weld position refers to a vertical weld position, where the meters are placed in a triangle-like configuration.
One of the main problems with vertical weld position is gravity. As you are welding against gravity, the molten metal tends to be pushed downwards. This can often lead to stacking and makes the vertical weld position more challenging than other positions.
Where is the 3F welding Position Used?
The 3F weld position is used in several different industries. Fillet welding is common in the fabrication industry, and is one area where you are likely to encounter 3F position. This position is also common in construction, especially when joining metals on corners. This welding position is also used in piping to join metal pipes together.
Characteristics of The 3F Welding Position
The 3F welding position is typically used for welding large weldments that cannot be easily moved due to their size. As such this position is performed on thick sheets of metal. A vertical weld can either be from bottom to top(vertical down) or top to bottom (vertical up).
The vertical up is more common. To achieve a good vertical weld, a reduced wire feed speed and voltage are recommended. This is to ensure the weld puddle does not become too fluid causing it to fall out or sag off the weld joint.
Ideally, even when welding thick sheets you should use a low heat input to counter the effects of gravity on the weld puddle. As for the rod angle, use a 45 degree angle for the 3F welding position.
Also, a straight motion is not recommended as this may lead to a ropey bead. Instead what you want to do is a zigzag motion or an upside down T motion. It is also wise to assume a comfortable position before welding in the 3F position.
What is the Qualification Range for the 3F position
So what welding positions can you use when you are qualified for the 3F welding position? The 3F welding position qualifies you to weld in all fillet positions from 1F to 4F. This applies to production pipe welding qualifications as well as production box tube welding qualifications.
How to Weld 3F Fillet with SMAW
For the purpose of this how-to section, we will be working on a ⅜ inch thick sheet of metal with 6010 rods. For the amperage, we will set it to 110 amps. As mentioned earlier for the vertical position we will use a rod angle of 45 degrees.
The First Pass
For the push travel angle, we will use a 5 to 10-degree angle. For this exercise, we use an inverted T motion. In this motion, you want to move the rod side to side and upwards then pause, and repeat this motion all the way up the joint.
This motion helps to flatten the puddle and fill in along the toes to prevent undercuts. The complete weld of the first pass should be flat with slight convex. You should also inspect for complete fusion along the toes.
The Second Pass
For the second pass, you want to place the rod on the toe of the first pass. You can also use the left toe of the first pass if you are left-handed. The work angle for the second pass should be 55 degrees.
The push travel angle should remain the same 5 or 10 degree angle. For the second pass use a whip and pause motion and overlap the root pass by about ½ to ⅔. The second pass weld should be flat to slightly convex.
The Third Pass
For the third pass center the rod on the left toe of the root pass. Reduce the working angle to 35 degrees. However, maintain the same 5 to 10 degree travel angle. Use a whip and pause motion and overlap the second weld by about ⅓. The finished weld should be flat to slightly convex.
The Pros And Cons of 3F Welding Position
Pros
Allows welding of large metal parts in the positions they are in without the need to move them
This welding position is a bit easier to accomplish than the 3G welding position
Fillet welding is common in many industries
You have the option to use either vertical up or vertical down welding
Cons
Takes more time to weld as a lower heat input is required to counter the effects of gravity on the weld puddle
Can be difficult to achieve since the weld is done against gravity.
3F welding Safety Tips
- Wear protective gear including a welding helmet to protect your face from the molten weld puddle
- Use a lower heat input to prevent the weld puddle from becoming too liquid which may lead to it falling off the joint.
- Make sure you are in a comfortable position before starting welding.
Is 3G the same as 3F?
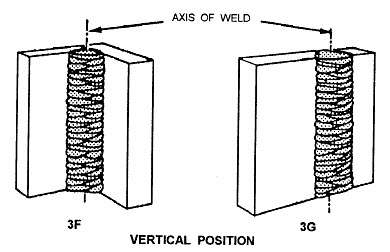
No, while both refer to vertical welding, the 3G position refers to performing a groove weld in the vertical position. The 3F position refers to making fillet welds in the vertical position.
Conclusion
The 3F welding position can be difficult to perform as you are welding against gravity. However, with practice, you can master this welding position. The most important aspects to take note of are the rod angle and the heat input as you want to manage the weld puddle and keep it from slagging out of the joint.