More often than not welding requires welding structures in the positions they are in. However, how some structures are positioned may make it difficult to weld. This has led welders to come up with techniques to weld structures that are weirdly positioned.
And this is why the American Welding Society provides four basic welding positions. These are flat, horizontal, vertical, and overhead. Each welding position has its challenges but in this article, we are going to be discussing the horizontal position.
In particular, the 2F welding position is a type of horizontal welding position. So what does this position mean?
All About The 2F position
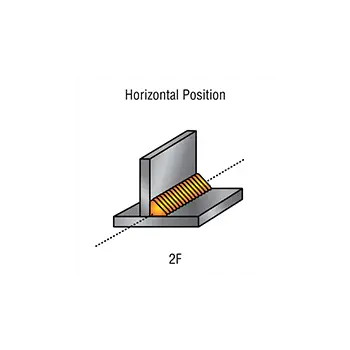
What is The 2F position?
The different welding positions outlined derive their names from how the weld face is positioned. In this regard 2 refers to the horizontal position. And this welding position can either be designated as 2G or 2F, with the G and F referring to groove and fillet respectively.
Thus a 2F welding position refers to a horizontal fillet weld. When welding in this position you will typically be welding on a nearly horizontal surface joined to a nearly vertical surface.
Where is the 2F position used?
The position is mainly used in the fabrication industry. It is also used in the piping industry for connecting flanges to pipes. In infrastructure projects, it is used as a replacement for bolts, as it offers a stronger joint.
2F Welding Position Characteristics
- A 45-degree welding angle is used when welding in this position to ensure the heat is focused on the area where the two pieces of the metal meet.
- The weld joint can either be a concave fillet or a convex one
- A 2F weld will typically have 5 parts, the root, toe, face, leg, and throat. The root is the part of the weld where the penetration is deepest. The toes are the two edges of the weld. The face is the outer part of the weld that is visible. The legs are the two sides of the metals being joined. The throat is the distance from the center of the face to the root.
Qualification range for a 2f fillet weld position
One fillet test on a ½ inch plate with the 2F welding position will qualify you for welding in both the 1 and 2 positions. There is no limitation on pipes with a 24-inch or above diameter for this qualification.
How To Weld in 2F welding Position
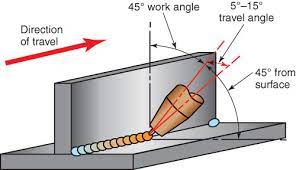
For this how-to section, we are going to be using a 718 rod on a ⅜ inch plate. The welder is set to 110 amps. And the first thing to do is make the first pass. Make sure you run it right in the middle making sure you tie in both sides of the metals.
After you run the first pass, the second pass should run right on the toe line of the first. Position the rod at a 45-degree down angle at the toe line. For the third pass, you want to angle your rod at a 35-degree or a lower such as a 25-degree angle.
When it comes to the 2F weld you want to get your angle right. If you do not use the right angle you could end up with too much weld bead on the bottom. Also depending on the thickness of the plate, you may have to run multiple weld beads.
For thicker plats, a total of 6 weld beads may be required to fully weld the joint together and avoid any problems with the weld joint. When making the fourth bead the angle of the rod should be at about 45-degree angle.
When you do the fifth the angle comes down to a 35 or 25 degree angle. Do this alternating of the rod when making multiple passes on the joint.
2F welding Position Tips
- Take note of the angle rod when doing a 2f weld. On the last passes, the angle should be lower at about 35 degree to avoid an undercut
- You want to maintain a tight arc when welding in this position. What this means is that you can almost feel the flux baked on the outside of the rod.
- Use a fan or a fume extractor or a snorkel hood, use it as a safety precaution to get the fumes from the weld away from you.
- When you need to do a restart strike the arc right in front of the crater where you stopped your last welding. For a restart, you want to weld back to the top of any weld strike formed before and not weld outside the weld zone.
Pros and Cons of the 2F welding Position
Pros
- This position gives a welder a clear view of the weld area, which makes it easy to clean and make high-quality welds.
- The easy access and view of the weld area also make it easy to prepare the weld area.
- The 2F welding position is one of the most used positions in different industries
- The 2F welding position is relatively easier to pull off than the 2G welding position
Cons
- This position requires a high heat output and it is easy to have a lack of penetration, especially for inexperienced welders
- It is not easy to detect defects in the weld joint with a simple visual examination
Is 2G similar to 2F?
The 2G and 2F welding positions are both similar in that they involve horizontal welding. However, they are not the same. The 2F position involves welding two metals together in a triangular shape.
The 2G position involves making a groove joint. In this weld position, the face of the weld is in a vertical plane. This position is harder to perform due to the position of the weld face, compared to the 2F welding position.
Conclusion
As mentioned, the 2F welding position is one of the most popular and is done in many different industries. As such it is an important welding position to learn. It is easier than the 2G welding position but does still take some time to master.