Aluminum is replacing steel as the construction material of choice in the automotive and other industries. As such, you are likely to find yourself having to weld aluminum more often than before.
While aluminum works well with most common welding processes, it is a whole other story when spot welding is involved. Aluminum is harder to spot weld than other metals, and most spot welders are incapable of getting the job done.
However, there is a way to spot weld aluminum.
How To Spot Weld Aluminum
Many people don’t know that aluminum can be welded. This is a tragic misconception. Aluminum welding requires skills and tools, but the benefits are well worth it. Spot weld aluminum is possible but not an easy task. it’s undoubtedly tricky work. Here I will discuss this tricky method briefly step by step.
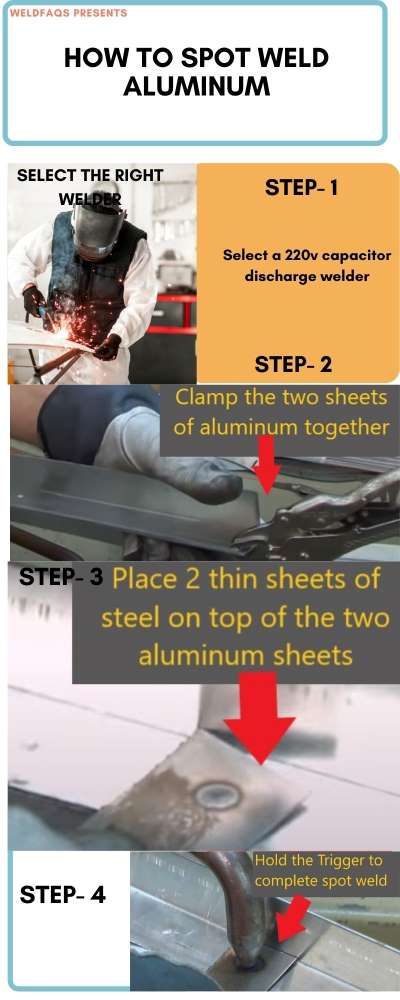
Step One: Get The Right Welder
A capacitor discharge welder that can store the high current needed for spot welding aluminum. You need at least a 220v to 240v welder which can deliver 150 amp output per phase as it’s suggested to use a three-phase electric power plug. A smaller welder of 120v will not be able to penetrate through the aluminum surface.
Step Two: Clamp The Two Metal Sheets
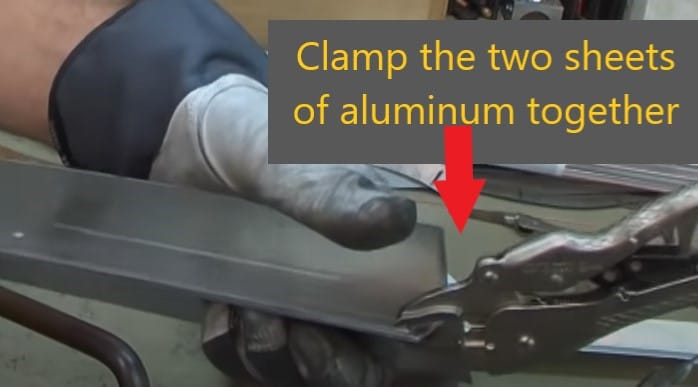
Spot welding involves welding two metal sheets together by using a high electric current. To prevent the two sheets from shaking or moving about, they need to be clamped. As such, the second step is to clamp the two sheets of aluminum together.
Step Three: Place Two Steel Sheets On Both Aluminum Sheets
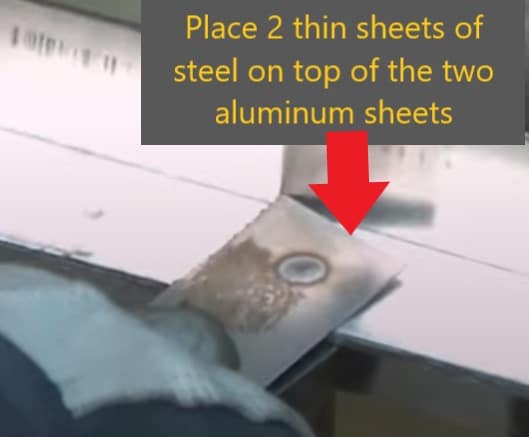
Now here comes the trick. Since we have established that spot welding aluminum is nearly impossible, we will need to improvise. Take two thin sheets of steel and place them on top of the two aluminum sheets you are welding.
Place the two steel sheets on the points where you want to apply the spot weld.
Step Four: Spot Weld
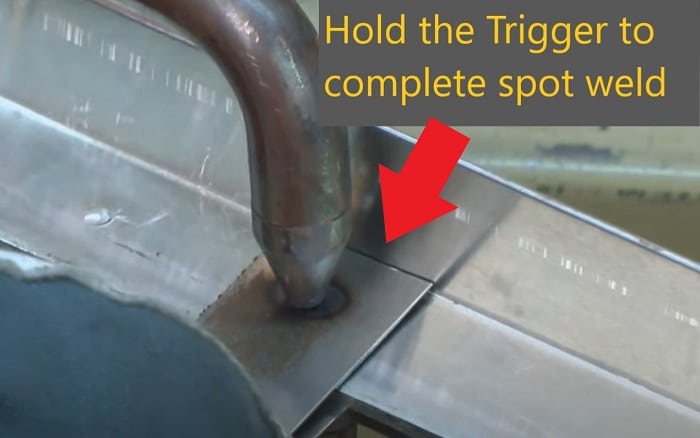
Slide the sheets in between the two electrodes of the spot welder. Ensure the two steel sheets are the ones that are in direct contact with the electrodes. By This spot welding, these two aluminum sheets stick with as tap joins.
Advantages Of Spot Welding
- Spot welding has a high production rate.
- It is possible to weld multiple metals at a go.
- it is possible to operate a spot welder automatically or manually
- It does not require a highly skilled person to operate
- It does not generate a high heat output meaning the base metal is not subjected to high heat.
Disadvantages Of Spot Welding
- It is only used to weld thin sheets of metal
- The cost of installation is high compared to other welding processes.
- This type of welding is vulnerable to metal deformation.
10 Tips for Spot Welding Aluminum
Spot welding aluminum is a process that can be done in many different ways. It’s important to know the various types of welds so you can choose the best spot weld for your project. Here are 10 tips for how to spot weld aluminum:
1) Aluminum will always have a dull finish where it has been spot-welded, while steel will not.
2) The edges of the metal should never overlap when they are being spot-welded.
3) When cutting through an area that contains spots welds, sparks should fly out and leave behind a black residue on your blade or cutter wheel.
4) If there is no residue left over after cutting through an area with spots welds, then the area may not be spot-welded.
5) The welds themselves should have a black appearance, while the metal around it will remain shiny.
6) When performing an acid etch test on aluminum that has been spot-welded to steel, there should only be traces of aluminum in the solution and no trace of zinc.
7) If you can’t find any sign of corrosion or oxidation on one side of the material but find it present deep inside the other side that was welded over top, then this indicates it is likely made from two different pieces that were spot-welded together.
8) Spot-welded aluminum must be on the outside of an item, and not inside where it can’t be seen.
9) If you want to try spot welding your own items, then make sure that you have a quality welder with plenty of experience in working with steel or other metals.
10 ) You’ll also need to do some research about the machine setup for this type of metalworking before even attempting anything; there are many different processes used depending on what is being welded together and how much stress will come from using this process.
11) Use a three-phase electric power supply for spot welding
12) Should weld faster than steel to avoid overheating
Can You Spot Weld pure Aluminum?
But first, can you spot weld aluminum? Technically speaking, spot welding 100% pure aluminum is nearly impossible. A thin layer of aluminum oxide forms on the surface of the aluminum.
This layer has a very high electrical resistance. Since spot welding relies on resistance heating, the layer of aluminum oxide makes it almost impossible. The high electrical resistance of the layer means a higher current is needed.
Conclusion
Spot welding aluminum is something many people have problems with. Spot welders are usually incapable of penetrating aluminum due to the formation of aluminum oxide. However, by introducing two steel sheets, you are able to bypass this problem.
It is far much easier to spot weld aluminum alloys. The latter is less likely to have a thin layer of aluminum oxide on the surface than pure aluminum.