Understanding the different types of welding processes and how they differ is not enough to turn you into a golden arm. To be a successful welder, you need to understand the different types of welds.
That being said, in this article, we will be looking at the most common weld types, their definitions, and how they differ.
1.Fillet Welds
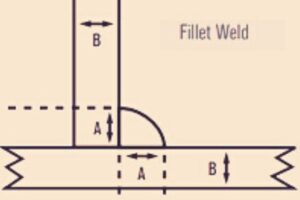
A fillet weld is a weld that joins two surfaces at an approximate right angle to each other.
Types of Fillet weld
There are three main types of fillet welds, these are;
-
Full fillet weld:
This is where the weld’s size is the same as the thickness of the thinner metal being joined.
-
Staggered intermittent fillet weld:
In this welding type, you create two irregular welding lines on a joint. An excellent example of this is a T joint. Here the fillet increments on one side are staggered compared to the other.
-
Chain Intermittent fillet weld:
Here, you have two lines of intermittent fillet welds either in a lap joint or T where the welds in one line are opposite to the lines on the other.
Uses Of Fillet weld
A fillet weld is used to connect two surfaces at a right angle.
Symbol Of Fillet weld
The fillet weld symbol is a right triangle on the reference line with the perpendicular line on the left.
Fillet weld procedure
The procedure of a fillet weld involves the positioning of the electrode at a 45-degree angle to the plate’s surface. Furthermore, the electrode should be tilted 15 degrees to the direction of the welding.
When welding thin sheets of the plate, there should be little or no weaving motion. However, for thicker sheets of metal, two or more passes are required with semicircular weaving motion.
Best for whom and why?
The fillet weld is considered more comfortable to use and less expensive than other weld types. This is not necessarily true, especially when it comes to ease of welding. This type of weld is common in steelworks applications.
2.Groove weld
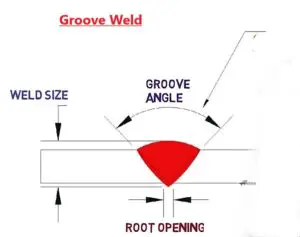
A groove weld is used to weld two materials on the same plane. This type of weld is typically used in a butt joint. Also, the weld may require preparation of the surface before welding.
Types of groove weld
There are six main types of groove welds, these are;
- J-groove: In a J-groove, one piece of the weld has a concave design while the other remains square
- V-groove: In a V-groove, the ends of both pieces are chamfered either doubly or singly
- U-groove: In U-groove weld, both weld pieces have concave ends
- Flare V-groove: This is used to weld two round or curved pieces
- Square groove: In a square groove, the weld pieces are usually tightly fitted and have slight separation between them.
- Flare bevel groove: This is used for joining two pieces, with one being rounded or curved and the other being flat
Uses Of groove weld
A groove weld is used to join two pieces together. This type of weld can be used on pipe welding.
Symbol Of groove weld
The symbol of a groove weld varies depending on the type of groove weld. Thus every kind of groove weld has a different symbol.
Groove weld procedure
Depending on the thickness of the metal, a groove weld can be achieved in a single pass. For more than a single pass, the slag from the previous pass has to be removed before making another pass.
Best for whom and why?
Groove welds are best for a skilled welder since there is a need for some work to be done on the metal before the welding. Also, groove welds require a bit more time and skill.
3.Plug Weld
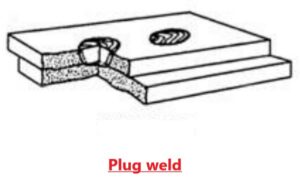
Sometimes called a rosette weld, a plug weld is used to join two metals together using a small circular hole. The metals are usually placed one on top of the other, with the top one having a circular hole.
Uses Of Plug weld
These weld types are used for repairing damaged metal surfaces and are predominantly used in the aerospace industry. However, it can also be used for joining two metal pieces together for use.
Symbol Of Plug weld
The symbol of a plug weld is a rectangle with a diameter symbol placed to its left. Alongside the diameter, a symbol will be a number denoting the diameter size.
Plug weld procedure
Plug welding will require preparing the metal first and then marking out on the top metal where you want to plug weld. If you will make multiple plug welds, the spots should be well spaced out.
The next step is to drill the holes where the weld will be deposited. You will want to clamp the metal together to prevent them from moving around as you weld.
When it comes to the actual plug welding, start from the outside and make your way towards the middle.
Best for whom and why?
Plug welding is mainly used in vehicle repair shops. It is an ideal weld for mechanics. The reason being it is used to tighten bolt studs permanently. Also, it works best for welding a rod that has to be inside a pipe.
4.Slot weld
A slot weld is somewhat similar to a plug weld in that both involve depositing weld material into a hole. In the case of a slot weld, you join two metals through an elongated hole. The hole can be open on one end.
Furthermore, it can either be partially or wholly filled with weld material.
Uses Of Slot weld
A slot weld is used to prevent buckling of lapped parts in construction. A slot weld can also be used to join components of built-up members in construction.
Symbol Of Slot weld
The slot’s width is given to the left of the diameter symbol, similar to a plug weld. However, in a slot weld symbol, the length and pitch that are separated by dashes are to the right of the symbol.
Slot weld procedure
The procedure of a slot weld is somewhat similar to that of a plug weld. In this case, two metal surfaces are joined together, on top of the other. However, with a slot weld, an elongated hole is used.
Best for whom and why?
Slot welds are used mainly in the construction industry. Generally, this type of weld is useful when you need to join two surfaces of varying thickness. This is because of the use of an elongated hole.
5.Flash weld
Flash weld is a type of resistance welding where the energy transfer comes from the resistance heat of the metals being welded. The metals are positioned end to end across a full joint area.
Uses Of Flash weld
Flash welding is used to make complex shapes ranging from bicycle rims to railway rails. This type of weld is also used to make components that are designed to be watertight.
Flash weld procedure
In flash welding, the two metal pieces are clamped together, and a flashing voltage is applied between them. When there is contact between the two metal pieces, a high-density current is generated, and their resistance heats up.
This process can be manual but, in most cases, done with semi-automatic or automatic welding machines.
Best for whom and why?
Due to this weld type’s complexity, it is best done by an experienced and skilled welder. This type of welding is used in industrial settings to make complex shapes and parts.
6.Seam Weld
A seam weld can be defined as the joining of two similar or dissimilar materials at the seam. In seam welding, an electric current, and pressure are used to fuse the two metal parts. This type of weld is similar to flash weld in that it is also a resistance welding technique.
Uses Of Seam weld
Seam welding is used in the making of fabricated metal products. Thus this type of resistance welding is used in industrial settings.
Seam weld Strength
A seam weld is a strong and durable weld since there is an application of heat and pressure. Also, the strength of a seam weld because of the amount of surface area that is joint.
Seam weld procedure
In seam welding, two metals are brought together to create contact. Then an electric current is passed through them. This leads to heat being generated between them, with the electrode controlling the flow of electric current.
Best for whom and why?
This weld type is used for making liquid tight metal containers. These can be vehicle fuel tanks, tin cans, and radiators. You can also use this type of weld for making and repairing exhaust pipes and barrels.
7.Spot weld
Spot welding involves joining two or more sheets of metal into one. This type of weld consists of the application of high heat and pressure. An electric current is passed through the sheets of metal to prevent resistance and cause fusion.
Uses Of Spot weld
Spot welding is a technique primarily used in the automotive industry to fuse two or more steel sheets. Other metals such as aluminum are challenging to spot weld due to them requiring high levels of electric currents.
Spot weld Symbol
The symbol of a spot weld is a circle that is placed above, below, or centered on a reference line.
Spot weld procedure
For a successful spot weld, the metal sheets being fused together have to be perfectly aligned, as it is impossible to align them when they are fused. A high voltage current flows from the electrode to the workpieces.
The heat needed to melt the metal is generated from the resistance of the base metals. When the current is switched off, the pressure is maintained as the workpieces cool down.
Best for whom and why?
This welding type is best suited to people looking to fuse two or more steel or titanium sheets. These kinds of metals work best with spot welding. As mentioned, this type of weld is not suited to welding aluminum.
8.Upset weld
In upset welding, two pieces of metal are joined together by the ends and fused using pressure and heat. It is another type of resistance welding.
Uses Of Upset weld
This weld type’s primary use is to weld metal rods and wires that have a small cross-sectional area.
Upset weld Symbol
The symbol of the upset weld is usually centered on the reference line. There is no need for the dimensions to be displayed on the weld symbol.
Upset weld procedure
This type of weld can only be achieved if the metals to be welded have the same cross-sectional size. Once this is done, the pressure is first applied, after which an electric current is passed through. Additionally, pressure must be maintained throughout the welding process.
Best for whom and why?
This type of weld is best for welding wires and rods with a small cross-sectional area. Thus, this type of weld is best suited for people crafting saw like appliances.
9.Flare bevel weld
This type of groove weld involves the welding of a rounded piece to a flat piece. This can be done for a joint between the two surfaces.
Conclusion
Different weld types are great for different instances. The weld type you choose will depend on what you want to achieve. The above are the most common types of welds.