Stick welding is a process known for producing a lot of heat. This can lead to burning through when welding thin sheets of metal. So does this mean you should not use stick welding on thin metal?
While MIG and TIG welding is recommended for thin metal welding over stick welding, it is still possible to weld thin sheets of metal with this process. And in this article, we will be looking at stick welding thin metal.
How to weld thin sheets of metal with a stick welder
Step one: Choose an electrode
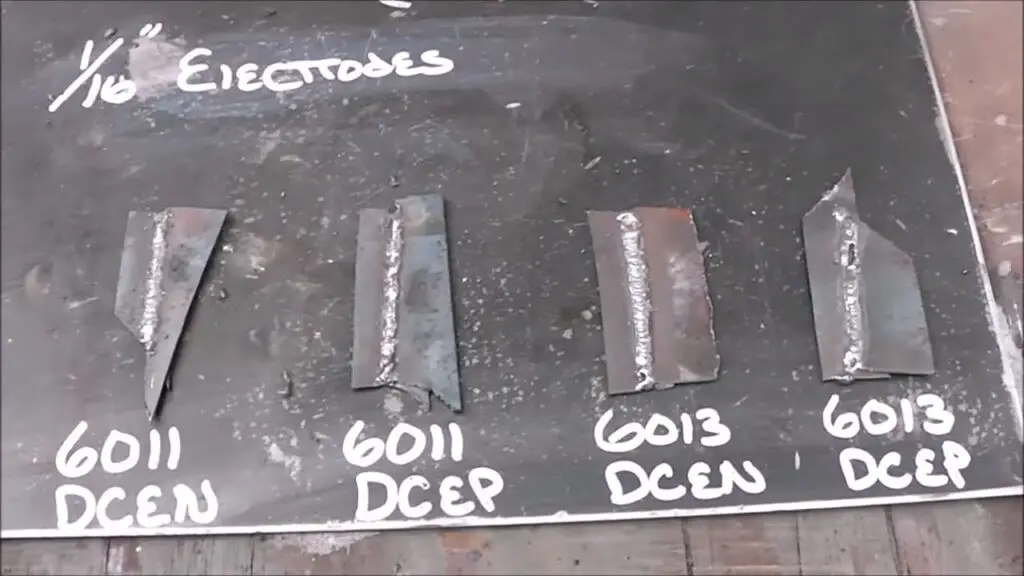
Stick welding thin sheets of metal requires an electrode that is both forgiving and has a high deposition rate. The best rods for the job can be either a ⅛ inch 6011 or a 6013 rod. If you are working with a surface with rust or paint then the 6011 is a bit more forgiving.
Step two: clean up the surface
While stick welding is known for being forgiving to rusted, painted, and dirty surfaces, it is always a good idea to clean the weld surface first. However, be sure not to scrub the surface too much as you may end up with no metal to weld.
Step three: set up the welder

For the best results, it is advisable to use a DC electrode negative. This means the electrode holder will be connected to the negative terminal of the welder. The reason for this is that it produces the least amount of penetration.
With thin sheets of metal, deep penetration is not always advised as this could lead to burning through given the metal’s thickness. As for amperage output start from the lowest amperage setting of your welding machine.
Step four: weld the metal
When welding the metal the best thing to do is strike it like a match. To avoid burn through, strike the arch and chip it away before striking it again.
Advantages of stick welding thin metal
- Stick welding is more forgiving on rusted, dirty, or painted surfaces than TIG and MIG welding
- Stick welding can be done outside in windy conditions
- Compared to TIG and MIG welding the equipment required is less expensive
- There is no need for external shielding gas with stick welding
Disadvantages of stick welding thin metal
- Produces a lot of heat which can cause burn through on sheet metal
- Stick welding produces a lot of spatter and slag
- The finished weld usually is not aesthetically pleasing
Stick welding safety tips
- Due to the heat produced by stick welding, it is advisable to wear gloves and other protective gear when welding
- Wear a welding mask to protect your eyes from ultraviolet light
- Ensure you are working in an environment free of clutter to avoid tripping over and falling
- When welding ensure you allow the stick welder to cool to avoid overheating
FAQs about Stick welding thin metal
Q-1: What is the best electrode for stick welding thin metal?
Ans: One of the best electrodes to use for sheet metal is the 6013 rod. This is a fast-freeze rod that works well on thin gauge steel. The 6011 rods are also recommended for welding thin gauge sheets of metal.
Q-2: What is the thinnest gauge metal you can stick weld?
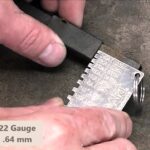
Ans: With stick welding, you can go as low as 22 gauge. At this gauge, you will mostly be doing a tack and skip kind of welding. Anything below 22 gauge and you will really struggle to weld without experiencing burn through.
Q-3: What metals can I stick weld?
Ans: Stick welding can be done on a variety of metals including mild steel, cast iron, low and high alloy steel, and carbon steel.
Conclusion
Stick welding is the perfect welding process for welding rusted, painted, or dirty materials. Thus while it is not the best for welding thin metal it is ideal when you do not have an option. This can be when you cannot properly clean the metal for TIG or MIG welding.