Milling and welding are two of the most common processes used in metalworking. So a confusion that many people have when it comes to metalwork is the difference between milling and welding. Needless to say, these two processes are very different in their execution and purpose. Welding is a process where two pieces of metal are joined by applying high heat, while milling involves cutting the metal with a rotating or reciprocating blade. In this article, we will explain the difference between milling and welding.
Before looking at the differences, though, it is essential to look at each process individually.
a quick explaination the Difference Between Milling and Welding!
Topic | Milling | Welding |
Tool Type | Rotating cutting tool | joining tool |
Working process | Cutting and shaping metal | Thermoplastics and joining metals |
How works | Using single or multiple rotating cutters to shape metal | Using high heats to melt the workpieces together |
Heat | Low heat | High heat |
Fire hazards | No risk | High risk |
Material wastage | Form of chip generation | No wastage |
Skill Requirements | High skill required | Semi-skilled also be preferred |
Set up cost | Higher | Comparatively lower |
Running cost | Lower | Comparatively higher |
Using area | Industrial sector | Widely use in any sector |
Milling, what is it?
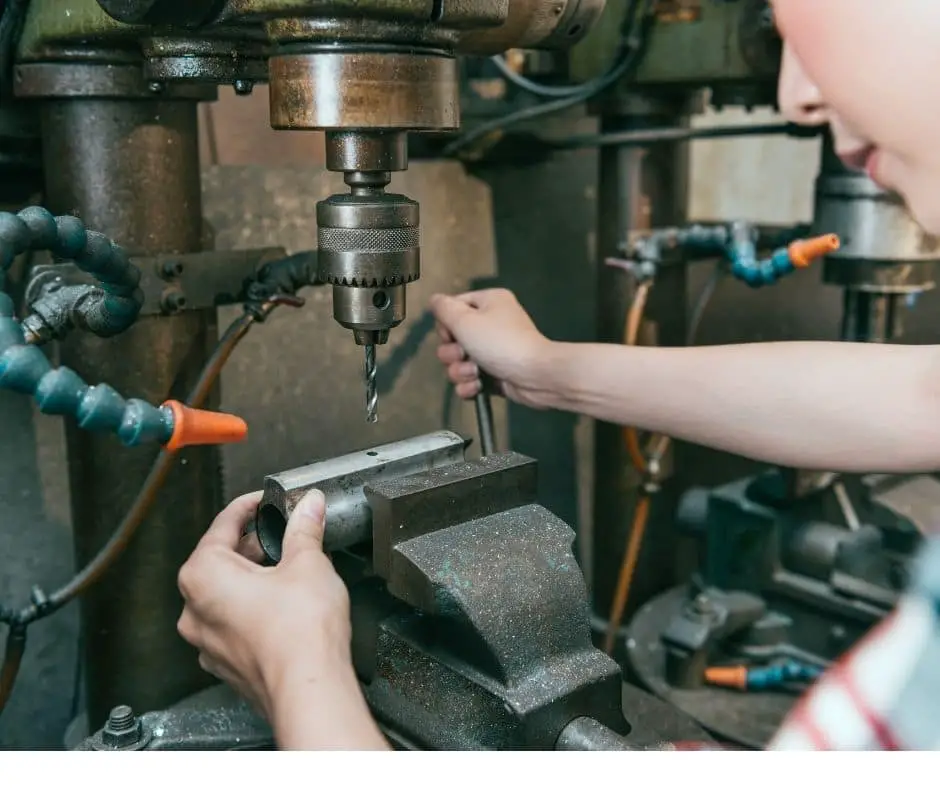
Milling is a process that involves the use of milling or cutting tools to remove material from the surface of a workpiece. The process typically entailed using cutting tools rotating at set speeds and brought in contact with the workpiece. The cutting tools start to remove materials when they come in contact with the workpiece.
What is this process used for?
Milling is used to remove crevices from the surfaces of metals that could cause corrosion. This process is also used to remove excess material off the surface of a workpiece. The process is also done to prepare metals for the application of corrosion-resistant coating.
The history of the milling machine
The history of milling can be traced all the way back to the early 1800s when milling machines were introduced to speed up hand-filing. Between the 1840s and 60s, there were a lot of production milling machines available.
However, these early models did not have the three axes of movement common in modern milling machines. Instead, they were similar to a drill press and were often positioned in a line where each machine performed a single operation.
The three axes design was first introduced in 1861 by Brown and Sharpe. This new milling machine, dubbed the universal milling machine, could mill complex geometries. Milling machines underwent rapid technological developments with the advent of WW1.
This continued even in the post-war period. And during WW2, Rudolph Bun now introduced the Bridgeport milling machine. The latter was lighter, easier to use, and cheaper than any other machine of the time.
The success of this machine inspired other similar designs, and by the 1950s, Numerical Controlled machines were being used. These used punched taps to direct the movements of the machines.
These were later superseded by the Computer Numerical Control machines in the 1960s and 1970s. Since then, milling machines have continued to be improved.
Types of milling machines
There are several types of milling machines. The main types are;
1. Plain or horizontal milling machine
As their name suggests, these machines have a horizontal spindle. The cutting tool is mounted on this horizontal spindle. This allows you to feed the cable in a vertical, cross, or horizontal direction.
2. Vertical milling machines
In a vertical milling machine, the spindle is perpendicular to the table. The spindle head is fixed to a vertical column that rotates at an angle. The cutting head is fixed to the spindle and is used to mill workpieces at an angle.
Some vertical milling machines allow for the adjustment of the spindle either upwards or downwards. These types of machines are designed for precision work.
3. Universal milling machines
These types of machines can perform all kinds of milling operations. They feature a table fitted with all motions and a dividing head with change gears. Also, the table can pivot at any angle up to 45 degrees in both directions.
These types of machines can also be used to perform helical milling operations.
4. Simplex milling machines
The spindle in this type of milling machine can only travel in one direction. Mostly, these machines can only travel in a vertical direction.
5. Duplex milling machines
Duplex machines are two milling machines positioned opposite each other. The two can either work independently as or as one machine with two simultaneous spindles. These types of machines can travel both horizontally and vertically.
6. Triplex milling machines
These types of machines have a spindle that can travel in all three axes, i.e., XY and Z.
The pros and cons of milling machines
Pros Of Milling machine
- Milling machines minimize chances of human error
- There are various customization options available
- It can be used to create complex shapes with the use of multi-tooth and single-point cutting tools
- It offers a more detailed finishing than other machines
- It is possible to manage operational costs when general-purpose cutting tools and equipment are used
Cons of milling machine
- Milling machines tend to be large and take up a lot of space
- Skill is required to operate a milling machine
What is welding?
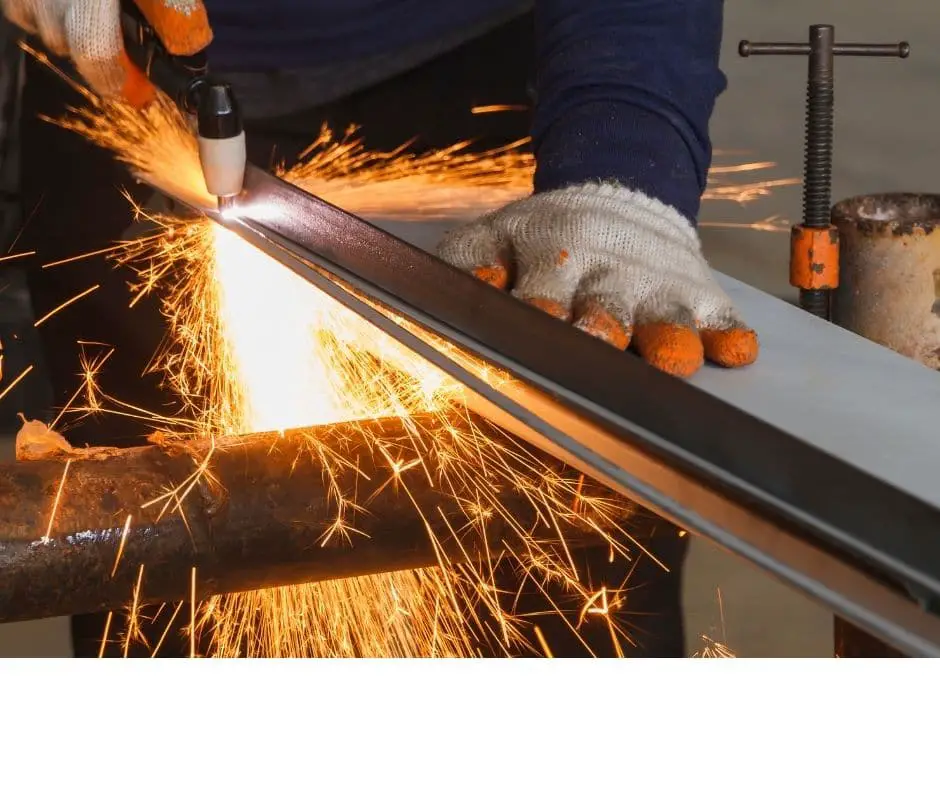
Welding is a process where two or more metallic parts are joined together by using heat, pressure, or both to form a uniform joint when they cool. While welding is mainly used on metals, the process can also be used on thermoplastics.
What is welding used for?
Welding is used to joining two or more metals to create one metal piece. Welding is also used in the fabrication of metal tools, ornaments, and parts. This process is also used to repair broken metal parts and the construction of industrial infrastructure such as piping.
Types of welding
There are four main types of welding processes; these are.
Gas metal arc welding (MIG)
This is a type of welding where a thin piece of continuous wire called an electrode is used. Shielding gas is also used in this process. The purpose of the shielding gas that is usually supplied through a separate tank is to protect the weld pool from contamination.
However, in MIG welding, you can also use thicker flux wires that have a coating that, when burned, releases a shielding gas, thereby not requiring a separate gas tank.
Shielded metal arc welding (STICK)
In this type of welding, an electrode heats up and melts into the metals being welded and fuses to form a joint. However, unlike with MIG, the electrode used in stick welding burns to produce a shielding gas to protect the weld pool for oxidizing with oxygen available in the air.
Gas Tungsten Arc welding (TIG)
As the name suggests, TIG welding uses a tungsten electrode. Due to tungsten being one of the toughest metals out there, it does not melt even in extreme heat. A second material is fed into the weld pool and melts to join the two metals being welded. This material is known as a filler material.
Similar to MIG welding, TIG also requires the use of a shielding gas such as helium or argon supplied from a separate gas tank.
Welding pros and cons
Pros of welding machine
- Welding results in a permanent joint
- When done correctly, the joint created through welding will be leakproof and strong.
- By Using welding, it is possible to join metals of various shapes
- This process can also be used to join plastic parts
- Welding does not result in changes in the cross-sectional area
Cons
- Welding can result in changes in metallurgic properties
- Welded joints do not do well under vibrations
Differences between welding and milling
Milling and welding are two very different processes. Milling is a machining process used to shed off materials from metal workpieces. On the other hand, welding is a process used to join two metal pieces.
Milling occurs when a metal worker cuts materials with sharp tools to create flat surfaces. Welding heats two pieces of raw metal together at high temperatures until they fuse together into one piece. Milling is essentially a cut-and-dry operation where welders will sometimes be asked to work with the equipment to make observations, but welding occurs over a much wider spectrum of tasks and can’t always require an expert for input. This means inexperienced workers might find it easier to get involved in this kind of profession or hobby than others like metal working or forging which often take.
Which process to use for what purposes
When you want to flatten the surface of a metal workpiece or remove crevices and other defects from the surface of a metal piece, then milling is the process to use. However, if you want to join two metal workpieces, welding is used.
Verdict
Although different, both processes are used in metalworking and fabrication. Furthermore, these two processes can be used together. Milling can be used to prepare metals for fabrication, while welding will be used for the actual fabrication works.