There are plenty of stick welding electrodes out there, with the vast majority of them being low hydrogen rods. And the subject of our article today is one such electrode the 7018 welding rod. This is a popular electrode preferred by many due to its low hydrogen content that protects against cracking.
However, that is not the only reason why the E7018 electrode is popular with many welders. Let’s take a closer look at this electrode, what it offers, what it does well, its chemical properties, and how to store it.
What Is The E7018 Electrode?
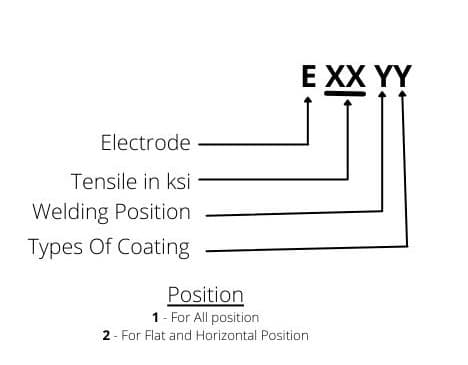
The E7018 is a low hydrogen electrode with an inorganic coating and with low-hydrogen iron powder coating. And like with other low hydrogen electrodes the 7018 can absorb water when kept in moist environments.
Though it will take some time for the rod to absorb water when you leave it in a damp or moist environment. Nevertheless, this is not to say that you should keep the rod in moist areas. As its name suggests this rod has a tensile strength of 70,000 PSI.
Additionally, it can be used in all positions. It has a higher deposition rate compared to some other low hydrogen rods. This is mainly because of its thicker iron powder coating.
Recommended 7018 welding rod at the best price
Mechanical properties of E7018
Tensile Strength | 70 Ksi |
Yield Strength | 58 Ksi |
Elongation | 22 % |
Welding Current | AC, DC (+) |
Coating Type | Low-hydrogen iron powder |
Welding Position | All positions |
Redrying temperature | 700-800 Degree Fahrenheit |
CVN @ -50°F | 20 ft•lbf (27 Joules) |
Welding Process | Arc Welding |
deposit composition of e-7018
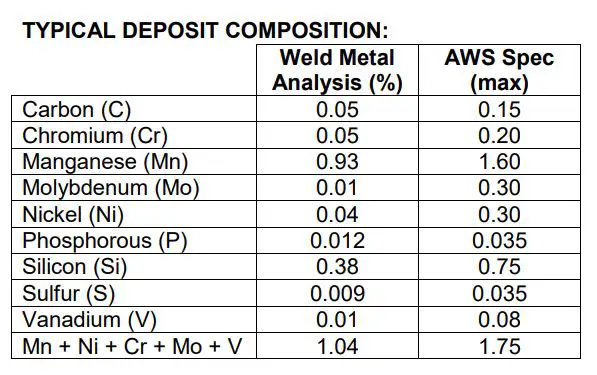
Weld metal | Carbon (C) | Chromium (Cr) | Manganese (Mn) | Molybdenum (Mo) | Nickel (Ni) | Phosphorous (P) | Silicon (Si) | Sulfur (S) | Vanadium (V) | Mn + Ni + Cr + Mo + V | Diffusible H2 |
Weld Metal Analysis (%) | 0.05 | 0.05 | 0.93 | 0.01 | 0.04 | 0.012 | 0.38 | 0.009 | 0.01 | 1.04 | 2.1 (ml/100gm) |
AWS Spec Max % | 0.15 | 0.20 | 1.60 | 0.30 | 0.30 | 0.035 | 0.75 | 0.035 | 0.08 | 1.75 | 4.00 (ml/100gm) |
welding parameters of 7018 welding rod
Diameter (inch) | Diameter (mm) | Polarity | Current (amp) | Deposition Rate (lb/hr) | Deposition Efficiency (%) | Optimal Amps | Volts |
3/32 | 2.4 mm | DCEP, AC | 70-110 | 1.8 | 62.7 % | 90 | 22.0 |
1/8 | 3.2 mm | DCEP, AC | 90-160 | 2.6 | 73.1 % | 130 | 26.5 |
5/32 | 4.0 mm | DCEP, AC | 110-230 | 3.9 | 62.5 % | 170 | 28.0 |
3/16 | 4.8 mm | DCEP, AC | 190-300 | 5.2 | 69.2 % | 250 | 28.5 |
7/32 | 5.5 mm | DCEP, AC | 240-340 | 7.3 | 69.7 % | 290 | 30.0 |
1/4 | 6.3 mm | DCEP, AC | 310-390 | 8.0 | 70.6 % | 350 | 32.0 |
The 7018 Welding Rod Features And Characteristics
- The rod has a smooth stable and quiet arc. Furthermore, it has low spatter levels, which minimizes the need for after-weld cleanup.
- It has a medium penetration level with a high deposition rate which allows you to add more filler metal into the weld in a short period. This is due to the thick iron powder coating.
- The rod contains carbon, chromium, manganese, molybdenum, nickel, silicon, sulfur, phosphorus, and vanadium. Manganese and silicon act as deoxidizers and help get through dirt or mill scale on weld surfaces.
- It has a good arc start and restarts, which is important in eliminating porosity problems at the start or end of a weld.
- The rod can be used with either AC or DCEP
What Is The 7018 Welding Rod Used For
7018 Welding Rod Applications
|
The Advantages And Disadvantages Of The E7018 welding rod
Advantages Of 7018 Electrode
- Since it is a low-hydrogen welding rod you will not have issues with cracking when using this rod
- Porosity problems are also minimal with this rod due to its good arc start and restart
- Has a good deposition rate that is higher than some other low hydrogen welding rods
- Can be used in all positions
- The low spatter levels of the rod mean you do not have to spend a lot of time cleaning up the weld after welding.
- Can be used with both AC and DCEP
The disadvantages
- Due to it being a low hydrogen rod you need to be more careful about storing it and should not be used in moist or damp environments.
- While it can be used in all positions it is not ideal for vertical welding.
- It has a medium penetration meaning you need several passes to weld thicker sheets of metal.
E-7018 Welding Rod Polarity And Amperage Settings
What amperage should you use with the 7018 electrodes? When it comes to the E7018 you want to increase the amperage by 30 amps for every 1/32 inch increase in thickness. Therefore, the thicker the electrode the higher the amperage.
On average, you can run a 3/32 inch electrode at an amperage setting of 65 to 100 amps. For a thicker rod such as a ¼ inch rod, you can set the amperage to 320-400 amps.
As for polarity, this rod is quite versatile and can be used in both DCEP and AC. You will get a good arc with both AC and DCEP thanks to the coating.
The Charpy V-Notch Impact Requirements For E7018 rod
Based on the AWS 5.1 specifications, the 7018 electrode requires a V-notch toughness value of 20 ft-lbf at -20 degrees Fahrenheit. The E7018-1 electrode, which is a designation of the 7018 electrodes used in low-temperature conditions, requires a toughness value of 20 ft-lbf at -50 degrees Fahrenheit.
Proper Storage Of the 7018 Welding Rod
The 7018 is sensitive to water and other contaminants. When exposed to water, the rod absorbs the water after a few hours. This leads to excess hydrogen and water is introduced into the weld, when you use the weld.
The water forms bubbles on top of the weld, weakening it. The weld bead will also look terrible. To avoid this you need to keep your rods in a welding rod oven. Set the temperature of the oven to between 250 and 300 Fahrenheit.
If you do not have many electrodes and are using them for a limited time you can opt for Lincolns hermetically sealed containers. These are the cheapest options available.
Preferable Welding Techniques
Welding position | Welding Technique |
Arc Length | Very short (less than half the diameter of the electrode) |
Flat | Angle electrode 10-15° from 90° |
Horizontal | Angle electrode slightly toward top plate |
Vertical Up | Use weaving technique |
Overhead | Use slight weaving motion within the puddle |
The E7010 Vs E7014 Vs E7018 Vs E7024
The E7010, 7014, 7018, and 7024 welding rods all have a tensile strength of 70,000 PSI. These rods have their differences though. The main difference is their flux coating.
As the fourth number in their names indicates these four electrodes have different coating types. The 7010 has a cellulose-sodium non-low-hydrogen flux coating. The 7014 and 7024 on the other hand have a titanium iron powder coating.
The 7018 as we have already seen has a low-hydrogen iron powder coating. Therefore, it is the only low-hydrogen electrode among the four. This means the other three have less strict storage requirements than the 7018.
Another difference is that the 7024 can only be used in two positions flat and horizontal positions. It is also a very fast rod and has a higher deposition rate and penetration. It is typically used to weld thick sheets where single pass welding is needed.
So when and where should you use each electrode? The 7010 is great for downhill welding. It is also great for root welding pipes and is commonly used in combination with the 6010.
The 7014 will be an ideal option for small projects and welding low-alloy carbon steel. It offers a higher deposition rate compared to the 7018. The 7018 is best suited for welding high carbon steel and structural steel.
The 7024 rod is perfect for welding thick and dirty metal surfaces. It has a higher deposition rate and penetration. It also has a thicker slug, which is relatively easy to remove.
E6010, E6011, E6012, E6013, E7018, E7028 Welding Rod Comparison Chart
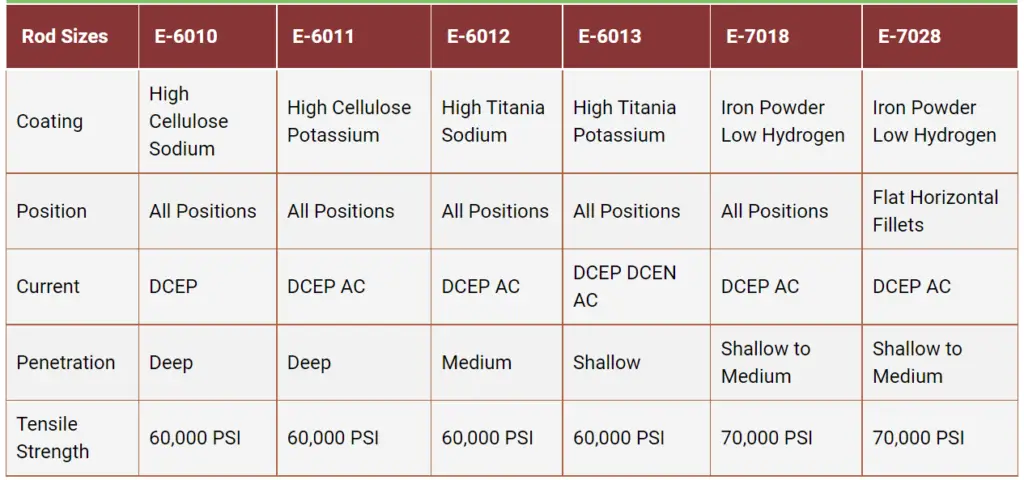
The E7018-H4R Welding Rod
The 7018-H4R is a designation of the 7018 that has a lower amount of diffusible hydrogen. This rod has 4ml of diffusible hydrogen at 100 grams. So what does this mean?
It means that this rod has a higher resistance to moisture absorption than the base 7018 rods. Therefore, it is not necessary to store it in an oven at 250 degrees celsius for 2 hours before use.
This rod can be used with both AC and DCEP and is used to weld carbon-manganese allow steels and high tensile heavy structural steels.
The E7018-H8R Welding Rod
The 7018-H8R rod is similar to the H4R designation in that it has a lower amount of diffusible hydrogen. In this case, it has 8ml of diffusible hydrogen at 100 grams. The R designation in both rods relates to their moisture-resistant properties.
It means both rods have been rated to be resistant to moisture when exposed to 80 degrees Fahrenheit. The rods can then survive in an environment with 80% humidity for up to 9 hours.
The E7018-1 Welding Rod
Another designation you will find of the 7018 is the 7018-1 electrode. The number 1 in the name means that the rod has a higher impact value. Therefore it can resistant to cracking at lower temperatures than the base 7018.
The impact value of the 7018-1 rod is 20 ft-lb at -50 degrees Fahrenheit compared to that of the base 7018 which is at 20 lb-ft at -20 degrees Fahrenheit. This rod is used in low-temperature environments, where the threat of cracking is high.
Why Are 7018 Rods Best For Structural Welding?
Applications involving structural steel require attention to heat input and are usually on strict timelines. Therefore welders need a rod that allows easy control over the arc, with minimal spatter.
The stable and quiet arc of the 7018 rod guarantees good control over the arc. Also, since the rod has a low spatter, there is minimal need for after weld cleanup. Thus there is less time spent cleaning up or reworking a weld.
How to stick weld with the 7018 in different positions
In most cases when structural welding you will be required to use all positions, horizontal, vertical, overhead, and downhill. When using the 7018, what you need to focus on is the current, angle, length of the arc, electrode manipulation, and speed of travel.
When it comes to the current you want to set the amperage to 125 amps for a start. You can bump up the amperage for a thicker rod. For this example, we will be using a ⅛ inch electrode.
For vertical up welding, you want to use a straight 90 degrees angle with a slight push and a tight arc. For the horizontal position, you want to use a drag technique with a 10-degree angle.
For the travel speed, you need to go slow enough not to leave undercut but also go fast enough not to build up too much metal. You also want to maintain a tight arc and not jam the rod into the weld puddle.
How to restart weld with 7018 in different welding positions
When restarting a weld with a 7018 how you tie it to the existing weld bead is important. Ideally, you want to use what is called a J technique. In this technique start slightly ahead of the weld bead and then come back to the end of the weld bead and over forming a J.
When you first strike a 7018 you can expect slight porosity as the flux doesn’t start shielding the weld immediately. This is why it is important to start ahead of the weld bead and then come back over it.
When you drag the rod back to the weld bead make sure the tie-in is inside the center of the weld bead. If the tie-in is too short you are going to have a gap, and if it is too big you are going to have a mound on the weld. This applies to the flat position but is also used in a vertical position.
Three Common 7018 Welding Rod Storage Mistakes
As we have already seen proper storage of 7018 welding rods is critical. Unfortunately, there is some misleading information out there on how to store these rods. Let’s take a look at four common misconceptions about storing these rods.
Storing The Rods In a Freezer
One of the most common misconceptions is about storing the rods inside a freezer. What some people do is wrap the rods in plastic bags and store them in a freezer. Now, this is wrong for a couple of reasons.
The main is that when you remove the electrode from the freezer for use, it will come in contact with the warm air outside. This will most certainly lead to moisture on the flux, which for a low hydrogen rod is never good.
Using Old Refrigerators
Welding rod ovens can be pricey, and to avoid spending money on one, some people have resorted to using old refrigerators fitted with a light bulb inside as an alternative. The problem with this is that there is no light bulb in the world that can provide temperatures of 250 Fahrenheit.
So an old refrigerator fitted with a bulb inside should never be used as an alternative to a welding rod oven.
Using Home Ovens To Re-bake Electrodes
Another alternative used by some welders is a home oven. In most cases, welders use it to re-bake their 7018 rods. As with the other two practices, this is wrong. Firstly, re-baking a 7018 requires temperatures of between 500 and 600 Fahrenheit. Setting your home oven at such high temperatures is a remedy for disaster.
How To Check If Your Electrodes Have Been Exposed To Moisture
Presence of porosity
The presence of porosity in the final weld is what will help you know if your rods have been exposed to moisture. If your rods have been left outside for some days without any direct contact with moisture you will notice minimal porosity in the final weld.
X-ray test
You may need to use an X-ray test to see the porosity. If the rods have been exposed to moisture, the porosity will be visible in the final weld. Also, you will notice cracking and the final weld bead will have a rough structure.
Cracking
The slag will also be more fluid and difficult to remove. In case of severe exposure to moisture, you will notice under-bead cracking and external cracking. You will also notice severe porosity along with a poor weld appearance.
how to Re-dry 7018 Electrodes
Re-drying or re-baking is the process of restoring electrodes to their original or near-original state when they are exposed to moisture. You need high temperatures to re-dry an electrode that has been exposed to moisture.
If the rod has been kept outside with no direct contact with water, re-drying will still apply. For this case, you need to re-dry the rod at a temperature of 700 to 800 Fahrenheit. In case of severe moisture exposure, you need to pre-dry the rod at a temperature of 180 to 220 Fahrenheit.
After pre-drying the rod you need to re-dry it at a temperature of 700 to 800 Fahrenheit. It is important to note that in some cases of severe moisture exposure, re-drying will not restore the rod.
How To Weld Vertical Up With 7018 Rods
Vertical welding is challenging as you will be fighting against gravity when welding. As such welding in this position requires a delicate touch and patience. If you decide to do a vertical up weld with a 7018 here is how to do it.
The weld shelf
Vertical up welding involves welding one small section and continuously welding above each section. Therefore each weld section acts as a base for the subsequent weld that you make. The lower bead is what is known as a welded shelf.
When welding the weld shelf the diameter of the shelf should be 1.5 to 2 times the diameter of the electrode. Thus if using a ⅛ inch electrode the weld puddle needs to be about ⅙ to ¼ inch.
Uses a zigzag back and forth motion when weaving vertically. This allows each weld puddle to freeze in place before you weld the next section.
Preventing Undercutting
One problem you will face when weaving vertically is undercutting. This is when the surface is gouged without enough filler metal. This is usually because of gravity drawing the filler metal away from the work surface.
To avoid this use a lower amperage and reduce your travel speed. You can use reduce the size of the puddle to improve control.
Use A Low Amperage Setting
The amperage you use should be low enough to allow the weld puddle to freeze quickly. If using a ⅛ inch 7018 electrode use an amperage of 120 to 130 amps.
Take Safety Precautions
With vertical up welding, the risk of falling molted metal is high. You need to take all safety measures seriously. This means having your safety glasses, helmet, and gloves. Also, wear long-sleeved and fire retardant clothing.
E7018 VS Other Welding rod sizes and their amperages
Rod Sizes | Rod Diameter | Amperage Range |
6010 | 1/8 inch | 75-125 amps |
6011 | 1/8 inch | 75-125 amps |
6011 | 3/32 inch | 40-85 amps |
6011 | 1/4 inch | 210-315 amps |
6012 | 1/8 inch | 80-140 amps |
6012 | 3/32 inch | 35-85 amps |
6013 | 3/32 inch | 40-90 amps |
6013 | 1/4 inch | 250-350 amps |
7014 | 3/32 inch | 80-125 amps |
7014 | 1/4 inch | 330-415 amps |
7018 | 3/32 inch | 65-100 amps |
7018 | 1/4 inch | 320-400 amps |
7024 | 1/8 inch | 100-160 amps |
7024 | 3/16 inch | 220-280 amps |
FAQs About 7018 Welding rod
It is not entirely accurate to call the 7018 a drag rod. Typically, drag rods tend to have a higher deposition and thick iron powder, a good example being the 7024. While you can use a drag technique in a flat or horizontal position. In other positions such as vertical up the 7018 cant be used with the drag technique.
6013 rods are considered great general-purpose rods and are mainly used for DIY works. 7018s on the other hand are used in structural steel applications and are used mainly by contractors.
In terms of ease of use, the 6013 has an easy-to-maintain arc with minimal spatter loss. Beginners are able to maintain and control the arc with the 6013. Thus in terms of ease of use, the 6013 is an easier-to-use rod.
Conclusion
The 7018 welding rod is used in various industries from bridge construction to shipyards. The rod has a lot of chemical and mechanical properties that make it ideal for these applications. It is a low hydrogen rod so how you store it will have a big impact on its performance and weld output.
Last update on 2025-08-30 / Affiliate links / Images from Amazon Product Advertising API