The 7014 is a popular welding rod known for its ease of use and thick easy-to-remove slag. This rod has good weld characteristics and can be used in all positions. But if you want to use this rod for your next welding project, it is wise to get to know its first.
So let’s take a deep look into the 7014, its characteristics, properties, and what you can expect from it if you use it to weld.
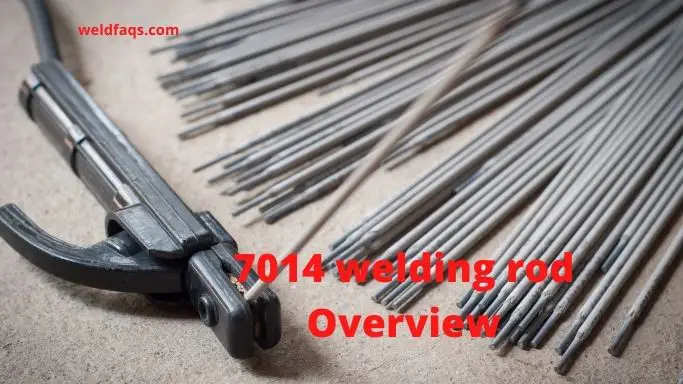
About E7014 Welding Rod
The 7014 rod is a carbon steel rod with an iron powder and titania flux coating. It provides medium penetration and is considered a fast-fill electrode. When you use this electrode, you can expect a tensile strength of 70,000 psi on the final weld.
Its iron powder titania flux coating gives it a high deposition rate and is generally an easy-to-use welding rod even for beginners. And is versatile in regards to polarity and can be used with AC and DC+ and DC-.
Mechanical properties of E7014
Tensile Strength | 70 ksi (550 MPa) |
Yield Strength | 58 ksi (460 MPa) |
Elongation | 17% |
Welding Current | DCEP, DCEN, AC |
Coating Type | Iron powder, titania |
Welding Position | All positions but not recommended for vertical down |
Welding Process | SMAW |
Best E7014 Welding Rod |
Buy welding rods at the best price on Amazon. Check here
welding parameters of 7014welding rod
Diameter (inch) | Polarity | Current (amp) | Optimal Amps | Deposition Rate (lb/hr) | Deposition Efficiency | Volts Range |
3/32 | DCEP, AC, or DCEN | 70-90 | 80 | 1.49 | 64.8 | 26-29 |
1/8 | DCEP, AC, or DCEN | 120-145 | 130 | 2.39 | 61.7 | 26-27 |
5/32 | DCEP, AC, or DCEN | 140-210 | 200 | 3.91 | 60.7 | 26-28 |
3/16 | DCEP, AC, or DCEN | 180-280 | 240 | 5.29 | 66.1 | 26-28 |
The 7014 welding rod features
So what are some of the notable features of this electrode?
- It has titania and iron powder flux coating different from a 7018, which has a low hydrogen iron powder coating.
- It has a tensile strength of 70,000 psi
- It can be used in all positions though it is challenging to use in the vertical downhill position
- It has a high deposition rate thanks to its flux coating
- Produces a smooth arc with minimal spatter
- It has a thick slag that is easy to remove
What is the 7014 welding rod used for?
7014 Welding Rod Applications
|
Advantages and disadvantages of the 7014 welding rod
If you decide to use this rod, you need to know its pros and cons. Let’s start with the pros.
The Pros Of E-7014
- The 7014 is one of the easiest welding rods to use, even for beginners who have little to no experience welding, and this is why it is popular for repairing farm equipment.
- Since it is not a low hydrogen rod, it does not have strict storage requirements like the 7018, it can also be used in moist or damp environments.
- It is an all-position electrode with a high deposition rate.
- It has medium to low penetration, making it a suitable choice for artistic welding, and it also produces beautiful weld beads.
- It has a fast travel speed and is a better choice for thinner sheets of metal.
The Cons
- While it can be used in all positions, it is not recommended for vertical welding as it lacks the fast freeze properties necessary for this kind of welding. For vertical welds, a 6010 or 6011 will be a better choice.
- It has a medium to low penetration, which is not ideal for welding thick sheets of metal. For thicker sheets of metal, you will be better served by a 7024 rod.
The 7014 welding rod amperage
This electrode requires an amperage range similar to that of the 7018. Therefore when welding with DCEN, you can set it at a low amperage of 100 to 145 amps. This is if you are using a ⅛ inch thick electrode.
However, if you are using AC, you need to crank up the amperage to between 110 and 160 amps. As with any other rod, thicker electrodes will require a higher amperage. You can use an amperage of 330 to 415 amps with a thicker ¼ inch welding rod.
Chemical properties of the welding rod
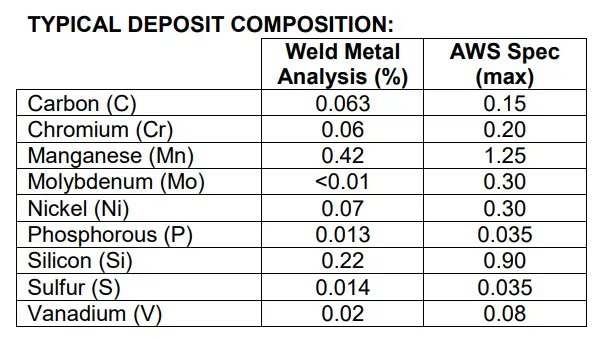
This electrode contains carbon, manganese, silicon, phosphorus, sulfur, nickel, chromium, molybdenum, and vanadium. The composition is 0.15 carbon, 1.25 manganese, 0.90 silicon, 0.035 phosphorus and silicon, 0.20 chromium, 0.30 molybdenum and 0.08 vanadium.
Welding techniques for E-7014 for different welding position
Arc Length | 1/8” or less |
Flat | Angle electrode 10-15° from 90° with higher heat than E6012 electrodes |
Vertical Up | Use slight whipping or weaving technique |
Vertical Down | Use higher amperage and faster travel, staying ahead of puddle |
Overhead | Use slight whipping motion |
Out of position welding | decrease amperage by 15% |
The e7018 vs. e7014
How does the e7014 rod compare to the e7018? These two electrodes are pretty similar in some regards. For starters, both offer a tensile strength of 70,000 psi, and both can be used in all positions but are not recommended for vertical welding.
But they also differ in some regards. The main difference is in the flux coating. The 7018 has a low hydrogen iron powder coating. And as we have already seen, the 7014 has an iron powder titania coating.
Because of this, the 7018 is ideal for welding high carbon steel and low alloy high strength steel. The 7014, on the other, is best for low alloy carbon steel. Also, the 7018 has a better fast freezing potential than the 7014.
However, the 7018, due to its low hydrogen coating, requires strict storage requirements. The rod absorbs moisture quickly and needs to be stored in an electrode oven. Also, it cannot be used in moist or damp environments.
The 7014, however, can easily be used in damp or moist environments without the need for storing in an electrode oven.
How to stick weld a multi-pass t-joint with 7014 welding rod
Step-1: Amperage setting
The first thing to do when stick welding a multi-pass T-joint with a 7014 is to set the welder’s amperage. We will be using a ⅛ inch 7014 rods for this exercise. The best amperage to set it at is 125 amps.
You can set it at 100 or 110 amps, but I found that it ran better at 125 amps.
Step-2: Make your First pass using Drag motion
Use a drag motion to make your first pass on the joint. Remove the thick slag covering the weld bead after you are done with the first pass.
Step-3: Make the second and third pass
The next step is to make the second pass. For this second pass, you want to point the rod down into the bottom toe of the weld and drag the rod at the center of the weld. For the third pass, point the rod up, pointing to the upper toe of the weld.
Storage and Reconditioning Temperature of e 7014
Storage Temperature at open place | 60°F to 100°F |
Storage humidity | Below 50% |
Storage Temperature in a oven | 100°F to 120°F |
Reconditioning Temperature | 250°F to 300°F (for 1 hr) |
FAQS about E7014 electrodes
Yes, the 7014 is not a low hydrogen rod and has better moisture tolerance than the 7018 and can thus be used in damp or moist environments.
One of the pros of the 7014 is that you do not need a rod oven to store the rods. You can use sealed containers to store the rods and protect them from contaminants.
Conclusion
The 7014 welding rod is easy to use rod perfect for beginners. It has a high deposition rate and works well on thinner sheet metals. It is also an affordable electrode and is versatile enough to be used in various welding applications.