The 6012 welding rod is a general-purpose rod known for its low penetration, stable arc, and high current. Because of its low penetration, it is mainly used for welding thin sheets of steel, but more on this later.
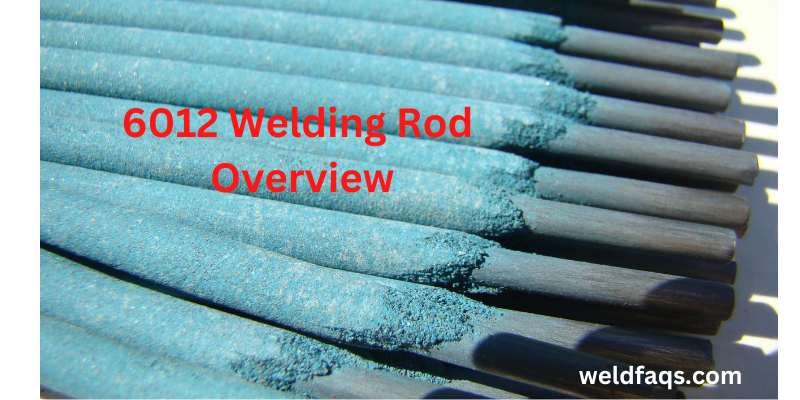
What is the E6012 rod?
The 6012 welding is a stick welding rod with a minimum tensile strength of 60,000 psi. It has a coating high in titania sodium. This coating is made up of clay and sodium silicate, which is used for binding. It also has calcium compounds in the coating.
As mentioned, this rod operates at a high current with minimal spatter. And as you may have guessed from its name, this is an all-positions welding rod. However, it is mainly used in the horizontal position.
Mechanical properties of E6012
Tensile Strength | 60 -70 Ksi |
Yield Strength | 48 – 61 Ksi |
Elongation | 26 % |
Welding Current | AC, DCEN |
Charpy V-notch at – 20 degrees | 65 |
Coating Type | High titania sodium |
Welding Position | All positions |
Welding Process | SMAW Welding |
deposit composition of 6012 welding Rod
Weld metal | Carbon (C) | Chromium (Cr) | Manganese (Mn) | Molybdenum (Mo) | Nickel (Ni) | Phosphorous (P) | Silicon (Si) | Sulfur (S) | Vanadium (V) |
Weld Metal Analysis (%) | 0.090 | 0.20 | 0.460 | 0.30 | 0.30 | 0.014 | 0.260 | 0.013 | 0.08 |
welding parameters of 6012 welding rod
Diameter (inch) | Diameter (mm) | Polarity | Amps (Flat) | Amps (V & O) | Volts |
3/32 | 2.4 mm | DCEN, AC | 65-100 | 65-100 | 19-25 |
1/8 | 3.2 mm | DCEN, AC | 85-130 | 85-130 | 20-24 |
5/32 | 4.0 mm | DCEN, AC | 110-160 | 100-150 | 19-23 |
3/16 | 4.8 mm | DCEN, AC | 160-220 | 120-190 | 18-21 |
The 6012 Welding Rod Features
- This rod has a minimum tensile strength of 60,00 psi with a yield strength of 48 kpsi
- The rod has an easy to strike and stable arc
- In terms of amperage, this rod requires a high amperage rating
- The weld beads created by this rod are usually smooth and uniform with minimal spatter and low porosity
- The rod has low penetration, and this is why it is mainly used on thin sheets of metal
- The rod can use in all positions.
The 6012 welding rod uses
- It is used in building construction for welding steel window frames.
- Also used in welding thin sheets of metal and for applications with poor fit-up.
- Used in general repairs and repair of farm implements
- Used in the fabrication of machinery and metal furniture
- Used to make ornamental iron ornaments and sheet metals
- Used to make lap fillet joints on the bottom of tanks
- It is also used in repairing and welding automobiles, ships, barges, pipes, rolling stocks, and railway freight cars.
Advantages and Disadvantages of the 6012 rod
The 6012 welding rod is a common welding rod that has a number of advantages that make it ideal for welding thin metals. However, it also has its fair share of disadvantages that make it an unideal option for certain applications.
Advantages Of 6012 Electrode
- The rod can be used in all positions
- It is excellent for the lap and fillet welding of sheet metals
- It is easy to clean off the slag
- It has excellent characteristics and operation for welding poor fit-up joints
- This welding rod is a perfect choice for beginners as it is easy to use
- Due to its low penetration, it works well on mild steel and thin metal
The disadvantages
- Due to its low penetration, however, it is only suited for welding thin sheets of metal
- It requires special handling and storage as it is vulnerable to water damage. It is recommended to ready the electrode for 60 to 90 minutes at 130 degrees Celsius.
Welding Rod Polarity and Amperage
This rod works with both AC and DCEN polarities. As for the amperage, as mentioned, it does require a high current. Thin electrodes of 3/32 inches can use between 65 and 100 amps, with thicker electrodes requiring an amperage setting of between 160 and 280 amps.
Charpy V-Notch Impact (toughness) Requirements for E6012 type electrode
The E6012 electrode has a Charpy V-notch impact requirement of at least 88 joules at 0 degrees Celsius. The impact requirements drop to 55 joules at temperatures of -20 degrees celsius.
E6012 rod Chemical and mechanical properties
The rod’s tensile strength is 60 Kpsi, while the yield strength is 58 kpsi. The elongation is 17% minimum. When it comes to the chemical properties of the rod, it has various chemical elements. These include carbon, manganese, silicon, sulfur, phosphorus, nickel, chromium, molybdenum, and vanadium.
In terms of composition, it has 0.20 carbon, 1.20 manganese, 1.00 silicon, 0.30 phosphorus, 0.20 chromium, 0.30 molybdenum, and 0.08 vanadium.
Differences between 6013 and 6012
Another electrode used to weld thin sheets of metal is the 6013. And as you might expect, it shares some characteristics with the 6012 rods. But the two rods also differ in some aspects. One area where the two differ is in the coating.
While the coating of the 6012 contains sodium, that of the 6013 contains potassium. In regards to polarity, both rods can run with DC positive. However, the 6013 runs better with AC than the 6012 electrode, which is another point of difference.
Both rods are used in the same applications as they are both excellent at welding thin sheets of metal, and this is what they were both designed for.
How to Weld with the E-6012
When welding with the 6012, the first thing to consider is the welding machine. While it can run with an AC welder, it works better with DC. So for this, we will use a DC Lincoln welder set to 75 amps. The rods we will be using is a 3/32 inch 6012 welding rods.
For the metal, we are using a 3mm ⅛ inch thick steel sheet. For the arc length, we want to maintain an arc length that is not larger than the diameter of the metal part of the rod. You want the arc length not to be long or too short.
For a fillet weld, you want to maintain a work angle of about 45 degrees to ensure you get the weld deposited evenly, even on the upper part of the joint. As for the travel angle, we want to maintain an angle of 10 to 15 degrees.
This helps push the slag back behind you as you weld. In terms of movement, you can do a slight weave, but ensure you are not going out of the weld pool.
Conclusion
The 6012 is mainly used for welding thin sheets of metal and is where it makes the most sense to use. Due to its low penetration, it cannot be used for welding thick metal. Also, the amperage needs to be high. When running with a lower amperage of, say, 60 amps, you will notice that it does not result in good fusion.