The 308 welding rod is a stainless steel rod used in welding different types of austenitic steels. It is a low-carbon rod with an iron coating that can be used with both AC and DC. So what exactly can you do with this electrode?
Although it welds austenitic steel types, including 201, 302,304, and 308 stainless steel sheets, it can also be used to weld dissimilar steel. In particular, it can be used to weld dissimilar 300 series steels.
All About 308 welding rod
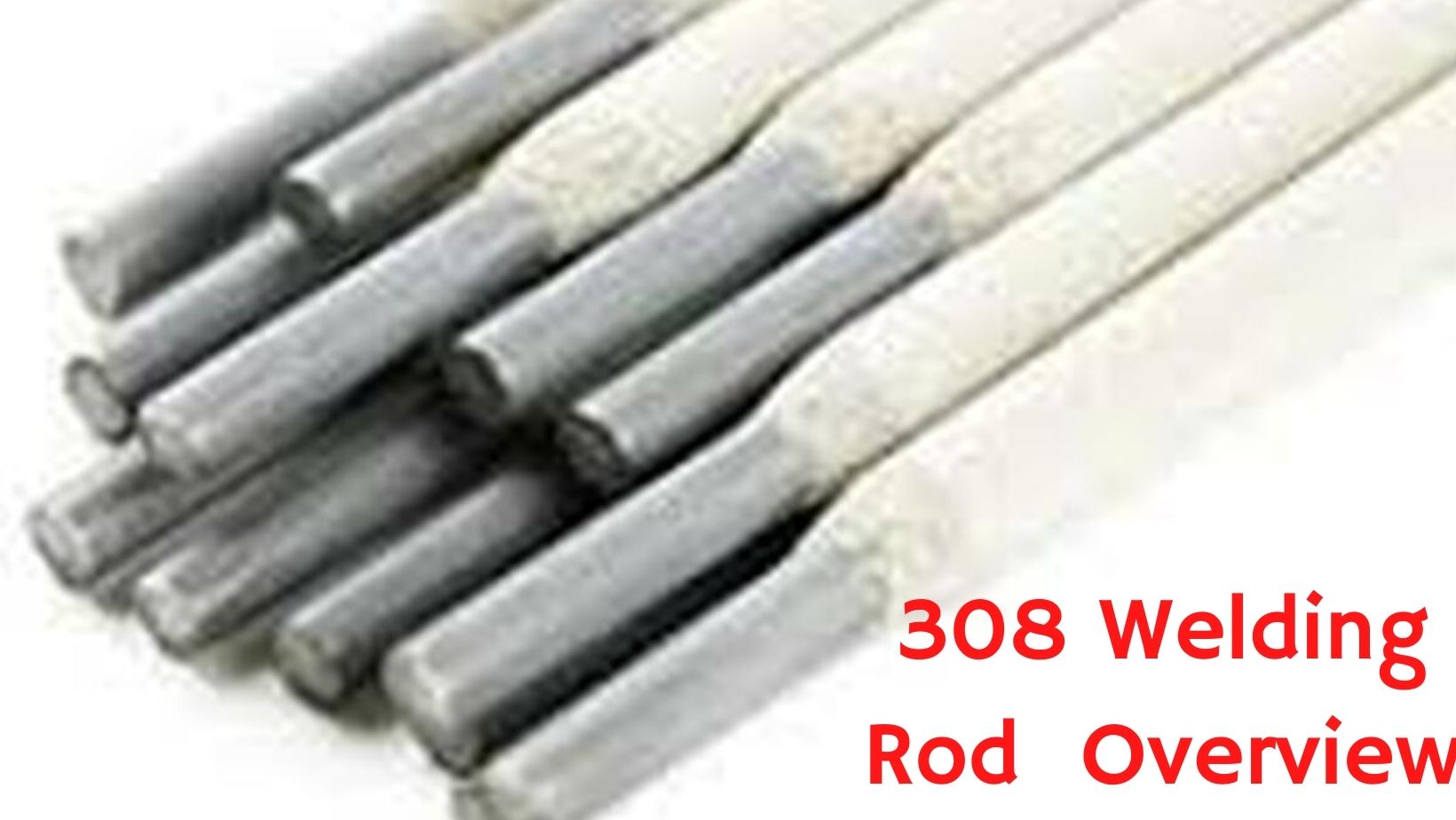
Mechanical properties of E308 rod
Tensile Strength | 90 Ksi |
Yield Strength | 66 Ksi |
Elongation | 45 % |
Welding Current | DCEP, AC |
Welding Position | All positions |
Coating | iron coating |
Best 308 welding rod | WeldingCity Stainless Steel 308 TIG Welding Rod |
deposit composition of er308
Weld metal | Carbon (C) | Chromium (Cr) | Manganese (Mn) | Molybdenum (Mo) | Nickel (Ni) | Phosphorous (P) | Silicon (Si) | Sulfur (S) | Copper (Cu) | Ferrite |
AWS Spec Max % | 0.03 | \20 | 1.7 | 0.1 | 10 | 0.03 | 0.5 | 0.011 | 0.1 | 6 FN |
welding parameters of 308/308L welding rod
Diameter | Current | Amp range (Flat) | Amp range (Vertical) | Amp range (Overhead) |
3/32” | DCEP or AC | 40 – 70 | 35 – 50 | 40 – 60 |
1/8” | DCEP or AC | 65 – 100 | 55 – 70 | 60 – 85 |
5/32” | DCEP or AC | 100 – 145 | 85 – 100 | 95 – 120 |
3/16” | DCEP or AC | 130 – 190 | 100 – 115 | 125 – 150 |
The 308 welding rod specifications
One of the reasons to use the 308 rods is that it gives a weld deposit with reduced carbon levels. This is important as it increases resistance against intergranular corrosion. But what are the 308 welding rod specifications?
Firstly, this rod can be used in both DC and AC. As for what is the tensile strength of the 308 welding rod? This rod has a tensile strength of around 58000 psi. And for amperage, it depends on the thickness of the rod.
Buy 308 steel welding rods at the best price on Amazon. Check here
The 308 Welding Rod Amperage
The 308 comes in several diameters running from 1/16 to 3/16 inches. There are also thinner rods of .035 and .045 inches in diameter. The amperage you use will depend on the diameter of the rod used.
The thicker 3/32 inch rods can use an amperage of 120-175 amps. Thinner rods will require a lower amperage, with a 5/32 inch rod requiring an amperage of 110 to 140 amps. For the thinnest rods, such as the 3/32 inch rod, you need an amperage of 70 to 85 amps.
The 308 Welding Rod Positions
The 308 welding rod positions are flat, fillet, vertical up, horizontal, and overhead, meaning it can be welded in all positions. It is particularly ideal for flat and horizontal positions because its flux coating allows for a smooth arc transfer.
The 308 Welding Rod Polarity
This electrode can be used with both AC and DC. When DC welding, it is used with Reverse Polarity or electrode positive polarity. It also works well with Alternating Current.
What gas do you use for 308 wire?
The 308 electrodes can use a shielding 100% argon shielding gas for TIG welding. For MIG welding, a mixture of argon and carbon dioxide is ideal. The best ratio is 2% carbon and 98% carbon dioxide.
You can also opt for a tri-mix of helium, argon, and carbon dioxide in the ratio of 90%, 7.5%, and 2.5%, respectively.
What are the 308 rods used for
- Used to weld low-grade austenitic stainless steel and 300 series stainless steels below the 308 grade.
- It can, however, be used to weld certain dissimilar steels; these are the 300 series of steels.
- It is the preferred rod for instances where the risk of cracking due to severe stresses is high.
- In terms of its industrial use, it is widely used in the chemical and food processing industry.
- It is also used in the food, beverage, and petrochemical industries for the general fabrication of stainless steel.
It is also used in construction jobs that use austenitic steel. There are different variations of this rod that are suited to different applications.
What Is The 308L welding Rod
The Er308L is a variation of the 308 welding rods with lower carbon content. The carbon content of this rod is held to a maximum of .03%. The purpose of this is to reduce the risk of intergranular carbide precipitation.
It is mainly used in welding in low-temperature conditions. This rod is typically used to weld 304L, 321, and 347 stainless steel metals.
Difference between the 308 and 308L welding rod
There is very little difference between the 308 and 308L welding rods. The main difference is in the carbon content of the rods. Of the two, the 308 has a higher carbon content, with that of the 308L being limited to a maximum limit of .03%.
Due to its lower carbon content, the 308L is used to prevent carbide precipitation. It is used to weld the 304, 304L, 308, and 308L stainless steel. However, it can also be used to weld the type 321 and type 347 stainless steel.
Difference between the 308 and 316 welding rods
Which one should you pick, the 308 or 316 welding rod? Well, it depends on the kind of steel you are welding. The 316 will be a better option for welding steel alloys with molybdenum. It contains silicon which makes the molten metal more fluid.
Thus the main difference between the two is the silicon content. The 308 has a lower silicon content compared to the 316. For this reason, it is not advisable to use it on 316 stainless steel.
The 308L 16 welding rod
This extra-low carbon electrode deposits a maximum of 4% carbon in the weld puddle. Due to its low carbon content, it is predominantly used to weld 304L, 321, and 347 stainless steel. It helps minimize the formation of chromium carbides and helps reduce the risk of intergranular corrosion.
Difference between the 308 and 309 welding rods
The 309 and 308 welding rods are both used to weld stainless steel. However, their chemical properties differ. The 309 has a higher chromium and nickel content of 22.0 -25.0 and 12-0 to 14.0, respectively.
This is compared to the 308 rod, which is 18.0 to 21.0 chromium and 9.0 to 11.0 nickel. The 309 also has a higher ferrite percentage. This rod is thus best suited to welding stainless steel to other types of steel, such as low carbon steel.
The 308 rods, on the other hand, are mainly used for welding austenitic stainless steel. Due to the higher ferrite content, the 309 is better at preventing chances of hot cracking.
Can I weld mild steel with 308L?
While it is possible, it is not recommended. The resulting weld joint may not have the corrosion resistance of the base metal. Also, there is a higher chance of hot cracking when you use it on mild steel. This is due to the rod’s low ferrite content.
Which filler metal should I use for welding carbon steel to stainless steel?
As mentioned, the 309 welding rod is better suited to dissimilar welding steels than the 308. When welding carbon steel to stainless steel, the best filler metal to use is the 309L. Using the 308 or 308L rods may result in a brittle weld joint.
Differences between E308L-16 and E308L-17
The E308L-16 and E308L-17 welding rods differ in terms of their coating. The 308L-16 version is thinner, while the 308L-17 has a thicker coating. The coating of the 308L-16 is a basic rutile coating and offers high resistance to hot cracking.
This rod can also be used in all positions and runs with both DC and AC. The 308L-17 variant, on the other hand, has a thicker acid rutile coating. It welds low carbon steel and is ideal for welding stabilized austenitic steels.
It is also used when the weld metal does not have to be similar to the parent metal. It is known for having low spatter, good arc stability, and a fast burn-off rate.
Conclusion
The 308 welding rod is used primarily for welding stainless steel. It is not ideal for welding dissimilar stainless steel though, due to its low ferritic content.