The 11018 welding rod is a low hydrogen electrode loved by the military. However, it isn’t a rod reserved for the military, and you can use it to weld steel. It works well with AC welders and can also be used for general fabrication works.
But should you pick the 11018 electrodes for your next welding project? Well, let’s find out with an in-depth look at some of the rod’s applications, specifications, and features.
All About 11018 Welding Rod
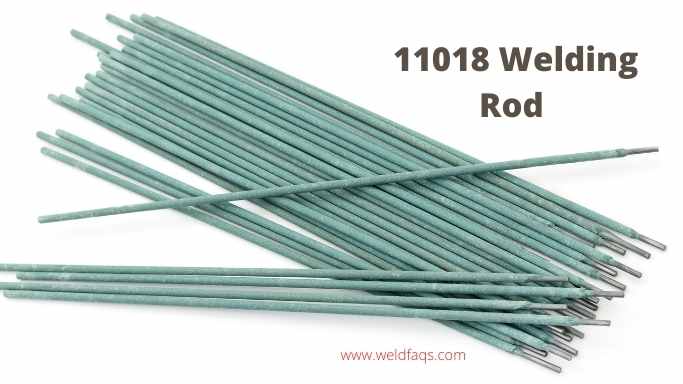
The 11018 welding rod applications
So firstly we need to know What are the common applications of this welding rod? This rod is used in a wide array of applications. These include;
- Welding HY-180, HY-90, HY-100, and T-1 steels
- General fabrication works
- Welding of rusted or dirty steel surfaces
- Repairing of farm and road equipment and wrought iron
- Repair and maintenance of piping and tanks
The meaning of the rod numbers
As with any other electrode, the numbers in this electrode’s name indicate its properties. The first number means that the rod produces welds with a minimum tensile strength of 110,000 psi. The following number is a 1, which indicates the 11018 welding rod positions. The rod can be used in all welding positions.
The last number, which is an 8, indicates the chemical composition of the rod. It is a low hydrogen potassium rod. It also has a powder coating on it. Also, while it works well with AC welders, you can use it with DC as well.
Mechanical properties of E11018
Tensile Strength | 100 Ksi |
Yield Strength | 98-110* Ksi |
Elongation | 20 % |
Welding Current | AC, DC (+) |
Coating Type | Low-hydrogen iron powder |
Welding Position | All positions |
Melting/Freezing Points | >2300 deg F |
Redrying temperature | 350-400ºC |
Welding Process | SMAW (Stick) |
Buy welding rods at the best price on Amazon. Check here
deposit composition as per AWS A5.5 requirements
Weld metal | Carbon (C) | Chromium (Cr) | Manganese (Mn) | Molybdenum (Mo) | Nickel (Ni) | Phosphorous (P) | Silicon (Si) | Sulfur (S) | Vanadium (V) | Diffusible H2 |
Weld Metal Analysis (%) | 0.04 | 0.19 | 1.57 | 0.29 | 1.99 | 0.015 | 0.34 | 0.01 | 0.01 | 2.00 (ml/100gm) |
AWS Spec Max % | 0.10 | 0.40 | 1.30-1.80 | 0.50 | 1.25-2.50 | 0.03 | 0.60 | 0.03 | 0.05 | – |
Tips on how to weld the e11018 welding rod
- The 11018 welding rod needs to be pre-heat before being used. Ideally, put it in an electrode stabilizing oven set to around 250 degrees Fahrenheit.
- Using an up and down motion for all welding positions apart from vertical up. For vertical up welding, a side-by-side motion will yield better results.
- Check the interpass temperature when welding to avoid cracking.
- You may need to increase the amps as the rod has a relatively sluggish puddle.
e11018 electrode Amperage and settings
The 11018 welding rod amperage and settings will depend on the thickness of the rod you are using. This rod does require a higher amperage. In this regard, a 3/32 inch 11018 rod will use a 75-115 amp range.
The thicker the rod, the higher the amperage required. Thus a 3/16 inch rod will use an amperage of 200 to 300 amps. Thicker ¼ inch rods will use 300 to 400 amps. The deposition rate also varies based on thickness.
While the thinner 3/32 inch rod has a deposition rate of about 2.0 lbs/hr, the thicker ¼ inch rod will have a deposition rate of about 7.8 lbs/hr.
welding parameters of 11018 welding rod
Diameter (inch) | Polarity | Current (amp) | Deposition Rate | Optimal Amps |
3/32 | DCEP, AC | 75-115 | 2.0 lb/h | 100 |
1/8 | DCEP, AC | 90-160 | 2.5 lb/h | 135 |
5/32 | DCEP, AC | 130-220 | 3.9 lb/h | 175 |
3/16 | DCEP, AC | 200-300 | 5.1 lb/h | 250 |
1/4 | DCEP, AC | 300-400 | 7.8 lb/h | 300 |
11018 welding rod using and storage tips
- Given its low hydrogen electrode, this rod has a low tolerance for moisture. Thus it is essential to store it in a dry place after using it to prevent moisture absorption.
- Storing it in an electrode rod and setting it to a temperature of above 200 degrees Fahrenheit before use is the way to go with this rod.
- For a hobbyist or a casual welder investing in a portable electrode, an oven is a good idea for storing your electrodes in
- When you buy an oven for your rods, avoid leaving the door open for long, as this can expose the rod to moisture and other outside contaminants.
- Also, store the rods in an upright position and in a single row to ensure they do not clash with other rods.
11018 welding rod chemical composition
As already mentioned, this rod is low in hydrogen. It has an iron powder coating and a 0.04 % carbon content. It also contains other metals, including chromium and phosphorous. The phosphorous content is 0.015%, while the chromium content is 0.19%.
What temperature should I heat my 11018 welding rod?
The 11018 rods should be pre-heat to a temperature of above 200 degrees Fahrenheit before use. Like other low hydrogen rods, the 11018’s coating absorbs moisture from the atmosphere very quickly. If not dried the water can break down into hydrogen and oxygen contaminating the weld pool.
Therefore the purpose of pre-heating this rod is to prevent hydrogen from coming into contact with the surface metal. This hydrogen will be a result of water particles on the surface of the rod.
The presence of hydrogen in the weld can cause the resulting joint to be brittle. It will also cause porosity and cracking and even result in distortions and deformities in the weld.
11018 welding rod vs. 7018 welding rod
The 11018 and 7018 welding rods are pretty similar in their use. Both require pre-heating and are low hydrogen rods. However, the 11018 requires a slightly higher temperature than the 7018 rods.
Also, the 11018 has a deeper penetration than the 7018 rods and a higher minimum tensile strength. As such, the 11018 rod works better on more rusty or dirty surfaces.
Conclusion
The 11018 welding rods do take some time to get used to, and some find it difficult to weld in vertical positions, but it is a good option for most welding tasks. It is particularly good for high tensile weld requirements and welding dirty or rusted surfaces.