Welding aluminum can be tricky due to its low melting point and high thermal conductivity. As such, not every welding rod is suited to welding this versatile metal. And to get the best result, you need to use an aluminum welding rod on Aluminum.
And one aluminum rod that is preferred by many for welding aluminum in instances where corrosion resistance is critical is the 4043 electrode. The rod is mainly used to weld aluminum alloys, including 5052, 6061, and 6063.
So what are some of its chemical properties and mechanical features that make the 4043 welding rod an ideal option for welding aluminum and aluminum alloys?
Mechanical properties of 4043 welding rod
Tensile Strength | 21,000-33,000 psi |
Yield Strength | 10,000-27,500 psi |
Elongation | 5-12 % |
Welding Current | DCEP |
Density | 0.097 lbs/in3 |
Welding Position | Flat, Horizontal, Vertical down, and Overhead |
Melting point/freezing point | 970 – 1515 °F |
CVN @ -50°F | 20 ft•lbf (27 Joules) |
Appearance, color | Silver grey |
deposit composition of e-4043
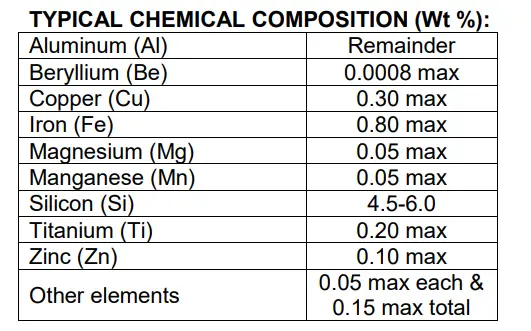
Weld metal | Aluminum (Al) | Beryllium (Be) | Copper (Cu) | Iron (Fe) | Magnesium (Mg) | Manganese (Mn) | Silicon (Si) | Titanium (Ti) | Zinc (Zn) | Other elements |
Concentration | 99 – 100% | 0.0008 max | 0.30 max | 0.80 max | 0.05 max | 0.05 max | 4.5-6.0 | 0.20 max | 0.10 max | 0.05 max each & 0.15 max total |
welding parameters of 4043 welding rod

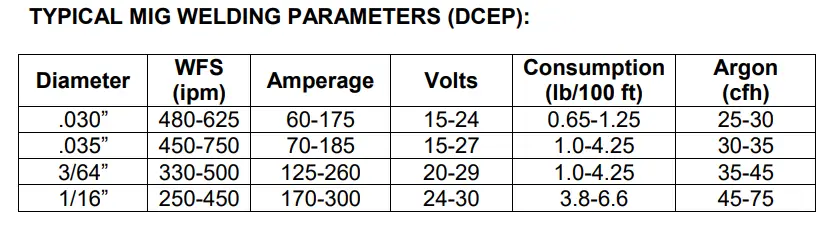
The 4043 welding rod specifications
One of the notable features of this electrode is its weld pool which tends to be more fluid than what you get with the 5356 rods. The fluidity of the weld pool is due to the 4043 welding rod having 5% silicon.
As for the welding rod’s positions can be used in four positions, flat, horizontal, vertical down, and overhead.
E4043 welding rod amperage settings
Aluminum rods typically run at a higher amperage than steel when it comes to amperage. The 4043 runs at an amperage of 60 to 275 amps. The thinner rods of 0.030 inches in diameter have an amperage of 60 to 175 amps. Thicker rods of 3/32 inches will have an amperage of about 275 amps or higher.
Given it’s an aluminum rod, it runs mainly in DCEP. The welding settings will depend on the thickness of the rod. For thinner, 0.030-inch rods, use a travel speed of 25 to 45 IPM. And if using a MIG welder, a 100% argon shielding gas will be ideal.
This rod can also be used to TIG weld and will use an amperage of 60 amps to 400 amps depending on the thickness of the rod. Argon as a shielding gas is also recommended when TIG welding with this electrode.
What is the 4043 welding rod used for?
The 4043 has many uses, especially applications that involve Aluminum. Some of the common uses of this rod are;
- Repair and making of housings and crankcases
- Manufacture of cylinder heads and blocks
- Used in making ornamental aluminum pieces
- Use in the fabrication of boats, trucks, and bus bodies
- Making of vats, tanks, and containers
- Underwater welding where resistance to saltwater corrosion is necessary
The 4043 welding rod’s general characteristics
As mentioned, the 4043 rod has a 5% silicon content. This makes the weld pool of these electrodes fluid. This result is that these rods typically use a higher voltage than other aluminum rods.
You will need about 25 volts and a wire feed speed of 38- inches per minute when welding with a 0.047 inch 4043 welding rod. The 4043 also produces a cleaner weld joint that does not require cleaning after welding.
For this reason, this rod is preferred over the 5356 rods for ornamental applications. The rod requires a 100% argon shielding gas for TIG and MIG welding. However, when welding thicker metal sheets, you can use a mixture of argon and helium.
Helium is a hotter shielding gas and offers a better penetration when added to the shielding gas mixture. The gas is quite pricey, though, and does not have quite as stable of an arc as argon does.
Proper storage and handling of the 4043 rod
Proper storage and handling of the 4043 rods are important if you want to keep your rods in good condition. The rods should be kept in a clean and dry environment. Furthermore, keep the rods in an environment with a temperature the same as that of the welding cell.
Keep rods used in MIG welding in the same plastic bag they came packed in. Alternatively, use a protective plastic cover. For TIG welding rods, keep them in the same box they came with to protect them against dirt and debris.
Aluminum welding rods are sensitive to moisture and oils. Wear gloves when handling these rods to protect them from the moisture and oils on your hands.
Can I weld Aluminum with steel rods?
No. Aluminum and steel have different melting points. Aluminum melts at a temperature of around 1200 degrees Fahrenheit, while steel melts at a temperature of 2700 degrees Fahrenheit. As such, when you use a steel rod on Aluminum, the Aluminum will melt long before the rod can even form a weld puddle.
Difference between 4043 and 5356 welding Rod
The main difference between these two rods is that while the 4043 has a 5% silicon content, the 5356 has a 5% magnesium content. This results in different weld properties between the two. The 4043 has the cleaner weld of the two.
The 5356 creates a layer of smut that needs to be removed after welding. Also, the 5356 operates at a lower voltage than the 4043. This results in a crackling sound produced by the 5356 when welding.
The two differ when it comes to wire feed speed settings as well. The 5356 requires a higher wire feed speed than the 4043. Both rods use a 100% argon shielding gas, though.
What are the most popular aluminum filler rods?
The 5456 and 4043 are the most common aluminum welding rods. These two are also widely used in welding aluminum and brazing aluminum alloys.
Can I use the 4043 rods to weld magnesium alloy aluminum?
It is not advisable to use the 4043 rods to weld aluminum-magnesium alloys such as the 5083, 5086, or 5456. The reason is the formation of magnesium-silicide that develops on the weld structure. This decreases the ductility of the weld and increases the chances of cracking.
Conclusion
The 4043 excels in situations where corrosion resistance is important. Also, due to its beautiful welds, it is perfect for ornamental applications. So if you want to weld Aluminum for ornamental or fabrication purposes the 4043 welding rod will be a better choice. On the other hand, 5356 rod is best suited to welding aluminum-magnesium alloys.