The 309 welding rod is an electrode mainly used for welding dissimilar metals. It is particularly ideal for welding stainless steel to mild or low alloy steel. It is a low-carbon electrode that is easy to strike an arc with.
There is of course a lot more you need to know about this electrode to know if it is right for you, which we shall cover in this article.
all about 309/309l welding Rod
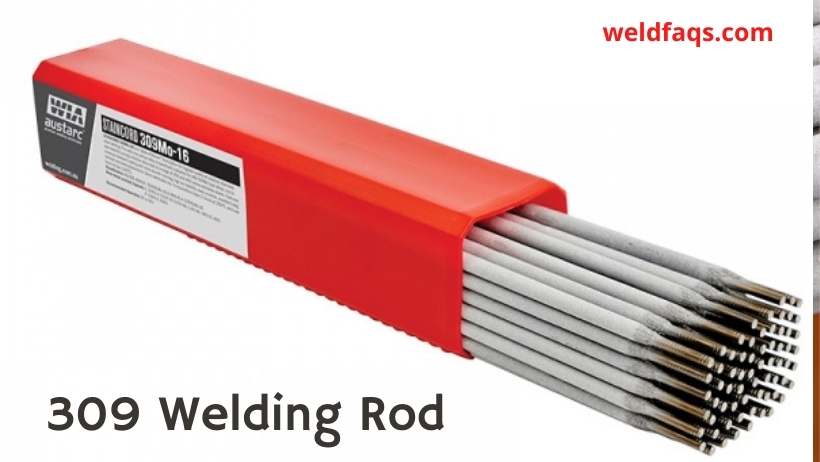
What is the 309 welding rod, and what is used for?
309 welding rod is an all-position electrode used for welding 309 type steel, mild steel to stainless steel, dissimilar steel such as 409 to 309, or 304 stainless steel. For its higher ferrite content, it is recommended for welding dissimilar metals.
In addition, 309 welding rod has a lower carbon content and a higher silicon content. This lower carbon content minimizes the risk of intergranular corrosion cracking, and silicon content works as a deoxidizer and helps remove weld impurities and increase weld puddle fluidity.
Mechanical properties of E309 rod
Tensile Strength | 85 Ksi |
Yield Strength | 55 Ksi |
Elongation | 40 % |
Welding Current | DCEP – Electrode+ |
Coating Type | Low-hydrogen silicon |
Welding Position | All positions |
Buy 309 steel welding rods at the best price on Amazon. Check here
deposit composition of e-309
Weld metal | Carbon (C) | Chromium (Cr) | Manganese (Mn) | Molybdenum (Mo) | Nickel (Ni) | Phosphorous (P) | Silicon (Si) | Sulfur (S) | Copper (Cu) | Mn + Ni + Cr + Mo + V | Diffusible H2 |
Weld Metal Analysis (%) | 0.03 | 23.00 | 1.05 | 0.10 | 13.50 | 0.020 | 0.45 | 0.016 | 0.10 | 1.04 | 2.1 (ml/100gm) |
AWS Spec Max % | 0.04 | 22.0 to 25.0 | 0.5 – 2.5 | 0.75 | 12.0 – 14.0 | 0.04 | 0.90 | 0.03 | 0.75 | 1.75 | 4.00 (ml/100gm) |
welding parameters of 309/309l welding rod
Diameter | Current | Amp range (Flat) | Amp range (Out of Position) | Voltage range |
3/32” | DCEP or AC | 70-90 | 65-80 | 20-23 |
1/8” | DCEP or AC | 80-110 | 75-95 | 21-24 |
5/32” | DCEP or AC | 120-160 | 100-120 | 21-24 |
3/16” | DCEP or AC | 120-160 | Not recommended | 23-26 |
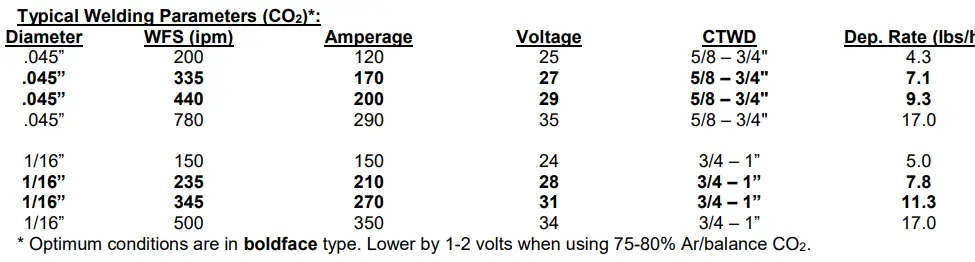
309 welding rod specifications
The 309 welding rod comes in several thickness sizes ranging from 2.0 mm to 4.0 mm. When it comes to the 309 welding rod settings it will depend on the thickness of the rod. The thinnest 2.0 mm electrode will require a 24-30 input volt.
As for the wire feed speed you set it to 80-240 inches/min. The thicker 4.0mm rod will require an input voltage of 30-36 volts while using a wire feed speed of 30-75 in/min. What about the 309 welding rod amperage?
The amperage setting of this rod will again depend on the thickness of the rod. The thinner rod uses an amperage of around 190 amps, while the thickest rod can use an amperage of 320 amps.
In regards to the 309 welding rod polarity, it works with both AC and DC current. This rod can also be used in all positions. As for what is the tensile strength of the 309 welding rod, it stands at 80,000 PSI.
309 welding rod applications
- Welding carbon steel to stainless steel
- Surfacing and building up components to increase wear resistance
- Joining stainless steel to mild or low alloy steel
- Welding of unknown steels
- Repair of lift truck forks and leaf springs
How do you weld a 309 stick rod?
309 welding rods are not the easiest to stick weld with and present a number of challenges. However, with the right technique, you can stick weld with these rods. Here are a few things to note when doing it.
When doing a joint weld it is important to note that the weld puddle created by this joint tends to be deceiving. At first glance it looks like it has a lot of build-ups, however, chipping away at the slag will reveal a flat weld bead.
Because of this, it is important to focus more on the sides of the joint and not the center. Focusing on the center too much can lead to it being heavy. When welding a long joint that requires you to use more than one rod how the different weld beads tie in is crucial.
Start welding from about ¼ inch from the previous weld bead to have a seamless connection with the new bead. After each bead chip away at the build-up formed to reveal the real weld bead underneath.
When not using 309 rods for TIG welding carbon steel
The 309 is used to weld stainless steel and carbon steel. However, there are instances when it’s not a good idea to use for tig welding carbon steel. 309 electrodes should not be used when welding tubes or pipes with high pressure.
Instances when you can use 309 rods for TIG welding carbon steel
There are other instances where it is okay to TIG weld carbon steel using the 309 electrodes. These instances include
- In instances where the carbon is pressed in the weld, the surface is enough to solidify the weld. Particularly when the weld surface will be machined later.
- When you need to top-up an opening that has pollutants that cant be washed
- If you are not sure about the type of steel a good example is when modifying a wrench
- When you need to weld any kind of stainless steel to carbon steel
- Where firmness is not a requirement in the weld
- If you suspect that the rod will hot break when welding carbon steel. This mostly occurs in transmission butt welds.
Difference between 309 and 309L
The 309 and 309L can be considered variations of the same electrode, however, they do have some differences. So what is the difference between the 309 and 309L electrodes? The main difference is the carbon content.
While both are low in carbon the 309L has a 0.03% lower carbon content compared to the 309. Thanks to its lower carbon content it is better suited to resisting intergranular corrosion, without the use of stabilizers such as niobium.
Directions for Using 309 and 309L welding rod
So when should you use one over the other? Typically the 309L rod is best suited for welding tasks where minimizing the carbide precipitation is required. This rod works well in welding stainless steel to low carbon steel as it helps minimize cracking. The 309 rods on the other hand are typically used to weld stainless steel to carbon steel.
Differences between E309L-15, E309L -16, and E309L -17
The 309 electrode comes in a number of variations based on the coating. The variations are designated by numbers ranging from 15,16,17 to 26.
The E309L-15
Electrodes with this designation have a lime-based coating and are used to weld in DCEP polarity. They have minimal slag compared to the other variations and can be used in all welding positions
However, electrodes that are more than 4mm thick are usually for flat and horizontal positions only.
The E309L-16
These electrodes have titania or rutile-based coating and can be used with both DCEP and AC. These electrodes have ionizing elements such as potassium, which are essential in stabilizing the arc in AC polarity.
The E309L-17
The e309L-17 electrodes have a silica-titania coating and are typically a modified version of the E309L-16 electrodes. As such, they can be used with both DCEP and AC polarity.
The silica in the rod increased the weld puddle’s fluidity, which helps improve the weld fluidity of stainless steel welds known for their sluggish puddles. These electrodes are also known for producing flat weld beads compared to the other two.
The E309L-17 rod is also known for having a slow freezing rod which makes vertical welding a bit challenging and requires more weaving.
Welding dissimilar metals using 309 stainless steel
When welding two dissimilar metals the 309 rods are recommended over the 309L or 309Lsi the 309 rods have a higher ferrite content that prevents weld dilution. This in turn reduces the chances of cracking.
Before welding, it is important to remove any impurities or mild scale from the surface of the metal. Stainless steel has an oxide layer that can cause difficulties when welding.
The gas you use will also be important the common 98% argon and 2% c02 combination may not be enough to allow for a proper weld bead. It is advisable to use a higher c02 mix for example a 90/10 argon and c02 mixture.
Frequently Asked Questions
When MIG welding with the 309 you can opt for a 100% carbon dioxide shielding gas. Alternatively, you can use a 75-180% argon/balance carbon dioxide mixture. Also, you can use a tri-mix with argon, carbon dioxide, and helium.
Overhead welding with the 309 can also be a little bit tricky. However, it is also manageable. You want to use an amperage of about 90 amps. However, if you notice the rod is glowing orange when you are halfway dial down the amps by about 10 amps.
When welding you want to position the rod at an angle so that the slag stays behind the weld puddle. Also, it is a good idea to lower your drag angle and be patient when welding with this rod. With the right settings, the slag will most likely self peel
Conclusion
The 309 rod is not the easiest to use and some people find it frustrating. However, it is a versatile rod that comes in handy when you need to weld dissimilar metals. It especially excels when welding stainless steel to carbon steel or low alloy steel.